KOH etching is a chemical process used for the fabrication of silicon nanostructures. This etching process has been studied extensively in both research and real-world applications.CSE provides individualized solutions for customers that want to use this process by using theKOH etching tank along with their existing wet bench equipment. All ofCSE’s KOH tanks are manufactured on site and built per your specifications. All PFA material is used for cleanliness and compatibility.
Definition of KOH Etching
Potassium Hydroxide (KOH) etching is a wet chemical etching process used to create cavities in silicon. Highly corrosive alkaline chemical compound (pH > 12) is used in conjunction with DI water and thermal regulation. The etch rate is limited; and the precision of Si etching is dependent on consistency throughout the nano chemical process. The process allows for the optimal precision of fabricating Si wafers. In addition, the KOH etching process can be automated for increased efficiency and reduction in cost.
Brief Overview of the KOH Etching Process
KOH etching utilizes wet bench equipment using PFA Teflon tanks. The anisotropic nature of Si etching offers increased flexibility and control after the process is established.The desired end product is impacted by the etching temperature; the percentage of KOH used; the implementation of crystal planes that act as a stop; the degree of anisotropy; the presence of any atomic defects in Si crystal; and the presence of other impurities naturally found in Si crystal. The doping concentration of Si has a notable impact on KOH etching; boron doped Si can also act as an etch stop if the boron doping concentration exceeds certain parameters.
Benefits of KOH Etching
KOH etching processes have notable advantages when compared to dry etching and other types ofsilicon wet etching process methods used to create nanostructures.
KOH Etching Benefits Include:
§ KOH is safe and easy to handle
§ Provides a repeatable process that etches fast
§ Lower cost compared to other etching processes
§ Superior fit for batch fabrication
Dry etching processes (Hydrazine) may pose notable risk of explosion and harmful toxins. Similar to KOH, Tetramethylammonium Hydroxide (TMAH) is an isotropic wet etching process. KOH etching is a superior process as TMAH etching is slower, and TMAH etching may result in the formation of hillocks.
Advantages of CSE’s Individualized Approach to KOH Etching
CSE’s KOH Silicon Etch Tank is designed to decrease impurities and unwanted byproducts due to advanced welding techniques with PFA sheet material. Continual adjustments to the Si etching process are not necessary after the initial process has been established. We construct all of our products per individual customer specifications, and we routinely design products that are compatible with a customer’s existing wet bench equipment.
A few notable CSE design features include the following:
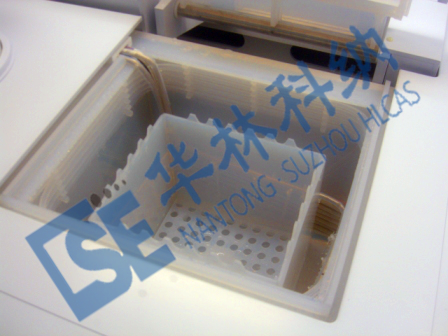
§ Manual cover with overlapping seal
§ Minimizes water lost
§ No concentration deficiency over long etch time
§ Water condensing system available on all baths (option)
§ Auto lid feature (option)
§ DI water or IPA spiking system available (option)
We take pride in never confining our customers to catalogue numbers, and we are the system integration specialists. If you need to utilize KOH etching in your manufacturing process, call us to discuss your specific requirements and get a quote
www.hlkncse.com ,400-8768-096;18913575037