
Wet Benches
湿法工作台的用途:
Purpose of Wet Benches:
Wet Benches are used in a wafer FAB to clean debris and/or to etch away unwanted or no longer needed films from wafers. They are also used to prepare a wafer’s surface for the next step in the overall process. Less sophisticated wet benches are often used in a FAB to clean quartz and other semiconductor equipment parts.
湿法工作台类型:
Wet Bench Types:
Wet Benches are generally manufactured for compatibility with Acid or Base chemistries. Base chemistry wet benches are often called Solvent Benches. You can recognize a Solvent Bench immediately because it's made of stainless steel. It will generally have integrated fire suppression due to the dangerous flash points of solvents. Acid wet benches are far more plentiful in the FAB and they are constructed of plastic.
Most FABs require acid wet benches to be made of Factory Mutual approved plastics
This fire-safe plastic is expensive but it is often required to qualify for insurance.
湿法工作台结构:
The architecture of a wet bench is one of multiple baths (tanks) sized to accommodate the submersion of a batch or “lot” of wafers. Typical batch sizes are 50 wafers or 25 wafers. Some common bench layouts are:
· In Line Linear - a linear series of process and rinse baths from left to right or vice versa.
· Rotary Benches - a single arm centered about three or four process baths
· Front to Back – usually a process bath in the rear and a rinse bath in front
· Once Through Bath – Rather than move wafers from bath to bath, wafers sit in a single bath while dilute chemicals are exchanged within that same bath. These tools are usually configured In Line Linear and are used in sophisticated factories.
参考网站:
Visit/Reference Website:
hlkncse.com
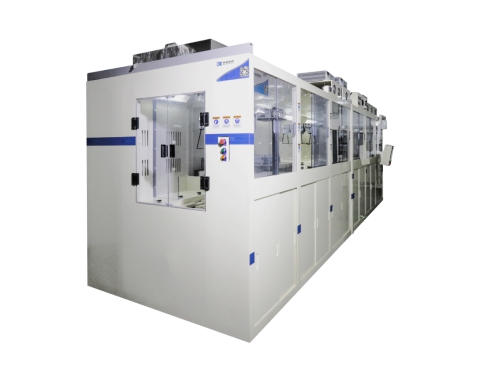
前道和后道:
FEOL vs BEOL:
FEOL (Front End of Line) refers to the manufacturing processes used to manufacture the transistor portion of an integrated circuit. BEOL (Back End of Line) refers to the manufacturing processes used to interconnect the transistors to one another and to the outside world.
When a wafer reaches the BEOL stage of production, the interconnect is constructed of metal, typically Tungsten, and Copper or Aluminum. Common FEOL chemistries are harmful to these metals making it necessary for Wet Bench engineers to embrace solvents for BEOL cleaning. BEOL will be discussed in detail (see Solvent Wet Benches).
前道清洗:
FEOL Cleaning:
A very important, sophisticated, and usually quite large wet bench used for FEOL cleaning is called a critical clean bench. It is also called the pre-diffusion clean (PDC), pre-furnace clean, RCA, or Standard Clean bench. This clean usually takes place just prior to a thermal, CVD, or ALD processes. Its effectiveness directly impacts the devices’ switching speed, so its critical.
Other common FEOL cleaning wet benches are:
1. Resist Strip
2. Nitride etch or strip
3. Residue clean, post etch, or post ash clean
4. Oxide etch
5. STI (shallow trench isolation) clean
These benches often incorporate cleaning in addition to their etching or stripping tasks making it difficult to offer up standard configurations. So, maybe it’s better to offer up some common chemistries instead.
常见的前道湿台化学:
Common FEOL Wet Bench Chemistries:
wetbenches001
1. SPM (Sulfuric Peroxide Mix) = H2SO4+H2O2+H2O also called Piranha is used to remove organics and to strip resist
2. DHF (Dilute HF) = H2O + HF used to remove native oxide and/or etch silicon
3. BOE (Buffered Oxide Etch) = HF with added buffers to slow down and stabilize etch rate
4. SC1 (Standard Clean 1) = APM (Ammonia Peroxide Mix) = NH4OH (Ammonia Hydroxide) + H2O2 (Peroxide) + H2O is great for removing particles, but has the unfortunate side effect of adding trace metal contamination. SC1 is therefore typically followed by SC2.
5. SC2 (Standard Clean 2) = HPM (HCl Peroxide Mix) = HCl + H2O2 + H2O used to clean and remove metallic contamination
6. Phosphoric (Hot Phos) = H3PO4+H2O typically boiling at 140C-160C and used to etch Nitride
7. IPA is the solvent used in critical wafer drying
湿法台清洗:
Wet Bench Rinses:
After each chemical bath, it is common to perform a DI water rinse. Sometimes the rinse is performed in the same chemical bath as the process. Other times, the rinse is performed in a separate rinse tank.
There are basically 3 major types of rinses and combinations of same:
1. QDR (Quick Dump Rinse) - Dumps the rinse water down the drain very quickly
2. Overflow Rinse – Rinse water is introduced from below the bath, forcing the water to overflow out of the bath and into a weir or drain
3. Spray Rinse – DI water spray bars are used to shower the wafers with rinse water
Rinse to Resistivity:
Rinse baths can be equipped with resistivity monitors. The resistance of pure DI water at 25C is some known number. If the rinse water is something other than that known number, we must assume there are contaminants still present, and we continue rinsing. This is a more scientific method of rinsing, in contrast to just a timed rinse.
Megasonics and Ultrasonics:
It is common practice that chemical baths and sometime rinse baths are equipped with megasonics or ultrasonics. Sonic energy creates cavitations that improve the cleaning efficiency of most chemistries. Harsh cavitation causes damage to the wafer. Generally, overly aggressive cavitation comes from ultrasonics frequencies, so megasonics are more popular.