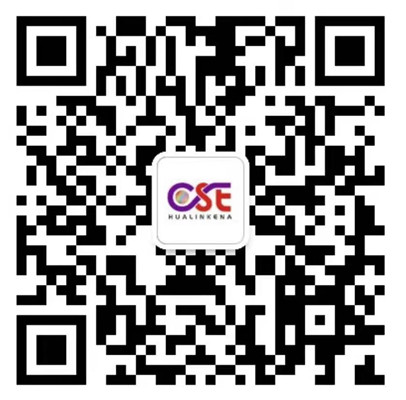
扫码添加微信,获取更多半导体相关资料
引言
本文在高真空组合工具中研究了气相预栅极氧化物表面制备:用无水氟化氢蒸汽和甲醇蒸汽蚀刻二氧化硅并通过改变晶片温度、室压和气体流速,这样就可以很好地控制氧化物蚀刻速率。本实验已经实现了氧化物蚀刻速率的5%的标准误差。在60/分钟的氧化物蚀刻速率下,每125毫米晶片产生的颗粒少于10个。原子力显微镜测量显示没有增加硅表面的微观粗糙度,这归因于蒸气氟化氢(HF)蚀刻。
介绍
现代集成电路(IC)制造中最重要的工艺之一是预栅氧化晶片表面制备。事实表明,金属氧化物半导体(MOS)器件的性能取决于栅极氧化物生长之前的清洁工艺。然而,在传统制造工艺中,每次工艺完成后,晶圆会在洁净室中从一个工具转移到另一个工具,因此会面临再次污染的风险。对于一些关键的工艺顺序,例如栅极氧化物生长,应该在晶片清洗后立即生长氧化物,以减少氧化物缺陷并获得高的器件成品率。
为了实现无污染制造,集群是选项之一。组合工具允许单晶片处理,在此期间,晶片在真空下在处理模块之间转移,并且降低了再污染的风险。配备原位诊断,可以更好地控制过程稳定性。随着晶片尺寸越来越大,单晶片加工变得越来越有吸引力。与真空兼容的气相清洁工艺目前正受到越来越多的关注。在气相过程中,氧化物和其他表面污染物可能会通过活性气体和表面层/污染物之间的反应而被去除。气相处理也具有清洁较小特征的潜力,因为湿法处理受到溶液表面张力的限制。气相处理的另一个优点是与湿法分批处理相比减少了化学品消耗。因此,气相处理是环境友好的。
例如,表1总结了从我们的研究机构收集的数据。数据显示了一个月周期的预栅极氧化物清洗过程的平均值。可以看出,除了HF以外,直接比较是困难的,因为两个方案中使用的化学物质基本上是不同的。然而,我们已经观察到在气相清洗中消耗的HF的量比在气相清洗中少大约六分之一湿法清洗,与湿法清洗相比,在湿法批处理过程中消耗了大量的去离子水,以及在气相清洗中消耗的化学物质的量很少。
除了气相处理本身的有效性之外,气相处理的成功取决于单晶片处理技术的大规模实施。我们在这篇文章和其他6–11中得出结论,气相处理对于预栅氧化清洗是有前途的。洁净室中微环境概念的采用将导致制造中更多的单晶片加工工具。这一点,再加上对危险化学品消耗和处理的更严格的规定,将加速该技术的实施。
在这篇文章中,我们报道了我们在高真空集成系统中对二氧化硅的氟化氢蒸气腐蚀和紫外辅助清洗的研究。我们提供了关于氧化物蚀刻、表面微观粗糙度、清洗过程中的颗粒生成和金属污染物去除的数据。我们还研究了栅氧化层的电学性质以及气相清洗和快速热氧化形成的SiO2/Si界面。这些结果已在最近发表的一篇文章中作了总结。
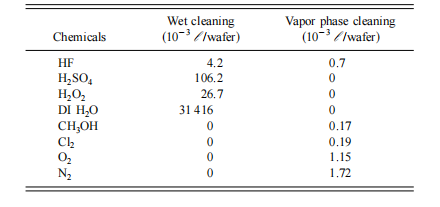
表1 传统湿法/批量清洗和汽相/单晶片清洗的化学消耗比较
通过让N2鼓泡进入室内。通过改变N2流速来调节甲醇的量。所有引入室内的气体都是半导体级的,并经过过滤以确保超高的纯度和清洁度。
结果和讨论
二氧化硅蚀刻
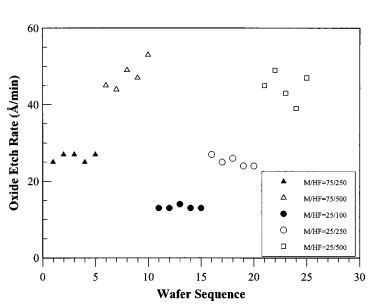
图4
为了找到工具给出最佳氧化物蚀刻性能的工艺窗口,进行了实验设计。实验的一个结果显示在图5中,其中氧化物蚀刻速率标准误差被绘制为氧化物蚀刻速率的函数。图中的每个数据点代表一个处理五个晶片的配方。蚀刻速率的变化随着蚀刻速率的增加而增加。存在一个可以实现小于5%的变化的工艺窗口。可以看出,其中三个配方已经重复和确认。通过仔细设计工艺,可以实现更小的变化。为了控制晶片之间的可重复性,蚀刻速率最好小于100/min。
表面形态
Si/SiO2界面粗糙度通常导致更高的漏电流或SiO2介电膜的早期介电击穿。14,15 Si表面微观粗糙度可以增加在HF蚀刻、化学清洗甚至去离子水冲洗过程中。15–18原子级光滑表面是形成栅极氧化物的理想选择。
如上所述,氧化物蚀刻速率在气相HF氧化物蚀刻工艺中波动。需要过蚀刻来保证完全去除牺牲氧化物。由于过度蚀刻造成的表面粗糙是不理想的。图6(a)是被蒸气HF侵蚀的Si(100)表面的AFM图像。蚀刻在50℃和200托的室压下进行3分钟,相当于60/分钟的氧化物蚀刻速率。该表面的均方根(rms)粗糙度为0.24纳米。作为比较,用100∶1的HF水溶液蚀刻Si(100)表面2分钟的结果显示在图6(b)中。这里,均方根值为
0.26纳米。因此,在蒸汽和含水HF腐蚀的Si(100)表面之间没有观察到差别。

图5 氧化物蚀刻速率标准误差是氧化物蚀刻速率的
二氧化硅蚀刻过程中的颗粒生成
在湿法清洗和去离子水冲洗过程中,颗粒可能会漂浮在液体顶部。当将晶片从溶液中拉出时,它们中的一些可能会重新沉积在晶片表面上。汽相处理的优点之一是不需要去离子水冲洗。
总结和结论
我们已经研究了气相处理在高真空组合工具中用于预栅极氧化物清洗应用的能力。对于50℃的温度和200托的处理窗口的室压,氧化物蚀刻是可再现的,晶片与晶片之间的标准误差小于5%。没有观察到增加的硅表面微观粗糙度,即使在侵蚀性的蒸汽HF蚀刻之后。在蚀刻速率为60/分钟的情况下,蚀刻过程中每个晶片大约产生8个颗粒。较高的氧化物蚀刻速率通常会导致较大的颗粒沉积。已经通过清洗程序证明了金属污染物的去除,包括蒸汽HF蚀刻,随后是UV/Cl2曝光。气相清洗技术是未来组合工具、单晶片加工发展的重要选择。