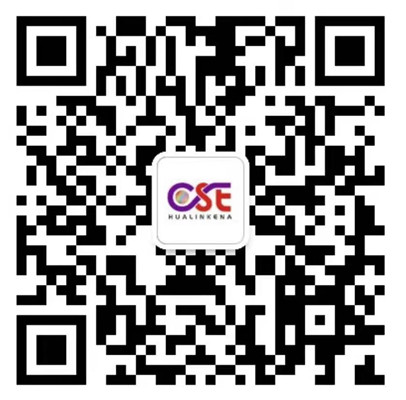
扫码添加微信,获取更多半导体相关资料
引言
本文研究了外延沉积前原位工艺清洗的效果,该过程包括使用溶解的臭氧来去除晶片表面的有机物,此外,该过程是在原位进行的,没有像传统上那样将晶圆从工艺转移到冲洗罐。结果表明,与不使用溶解臭氧作为表面处理的工艺相比,溶解臭氧显著提高了产率。另外还表明,稀释化学物质和原位高频/干燥是先进IC制造中成功沉积晶圆加工所需的关键因素。以下研究提供了证明在干燥机中一步稀释现场高频的数据和过程。
实验
所有实验都是在Naura-Akrion的GAMATM自动湿站上进行的,该站能够执行多罐序列和单罐原位过程。在外延生长步骤之前,硅片在工具中进行处理,用于进行外延前清洗。裸硅晶片用虚拟氧化物晶片处理,交替或夹心,以模拟图案晶片的情况。为了抵消高水平的污染过程,采用了多种清洗技术,并与传统的多罐方法进行了比较。使用的材料是:配备GAMATM湿工作台的LuCIDTM干燥机(高频控制注射),KLA-Tencor表面扫描(≥0.12µm检查),低颗粒计数的裸硅晶片和热氧化物晶片。浓度和参数:100:1HF(23oC)、400:1dHF(23oC)、1:2:50dSC1(50oC和800W)、DIO3冲洗(23oC下~5-10ppm)。
结果与讨论
典型的标准工艺是使用高温的h2预烘烤来分离晶片上的天然氧化物,以为外延层沉积准备表面。然而,需要较低的温度来确保这些先进的下一代设备的等温处理。在IC制造中,晶片通常与氧化物晶片混合或使晶片形成图案,并且暴露的硅通常与氧化物或氮化物区域相邻。当仅使用裸硅晶片时,传统的hf-last工艺也产生了低粒子添加量;即在0.12µm时,平均粒子添加量小于40个粒子(图3)。此外,外延后缺陷也很低(~1.26缺陷/cm2)。
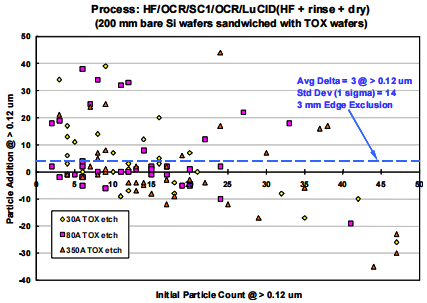
图3
硅晶片被夹在氧化物填充晶片之间,以模拟典型制造环境中的图案晶片。常规的HF最后一种工艺(SC1/Rinse/HF/Rinse/Dry)在0.12µm(>1000),高的外延前外延颗粒计数也导致高的外延后外延缺陷(>30000),颗粒缺陷通常被认为是外延沉积过程中外延缺陷的成核位点。传统的晶片转移方法在由于晶片通过液对空界面而增加硅酸盐颗粒在硅表面的沉积方面起着重要作用。为了抵消硅酸盐的沉积,我们测试了两种不同的方法。因此,为了防止晶圆穿过污染物所在并沉积在晶圆表面的液体对空气界面,我们开发了一种原位工艺。在干燥器中使用高频化学注入来进行原位过程,由于晶圆没有穿过液对空气界面,产生了更低的颗粒沉积。图3和图4显示了平均粒子加数小于50个粒子的结果。
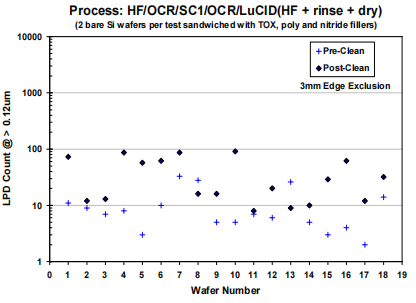
图4
在臭氧级联冲洗(OCR)中化学生长的氧化物足够稳定和厚度(7-10A)以保护硅表面免受金属粗糙化的任何影响,原位方法的后外延清洗结果,每个晶片的平均LPD密度约为0.89个缺陷/cm2,另外表明,hflast缺陷越低,外延沉积缺陷越低。
每个不同的清洗配方的结果在之前都被总结过。测试结果表明,实现极低的外延后沉积缺陷,最关键的步骤是在步骤之间不需要晶片转移的原位过程,为了表征背景氧化物的厚度,测量也作为晶片表面氧含量的指示器,同样重要的是要注意,晶片表面的氧含量可以显著增加晶片上的后外延缺陷的数量。h-钝化表面的氧含量越低,晶片表面的后外延缺陷量就越低。
溶解臭氧(DIO3)可用于许多不同的过程,如;氧化物再生、光致抗蚀剂和有机污染物的去除和前栅极清洗。这里的臭氧可以用来在高频清洗后的晶片上重新生长氧化物。在环境温度下,在不同臭氧浓度的去离子水中,氧化物厚度与时间的关系。溶解的臭氧可作为硫-过氧化物混合物(SPM)的替代品,以有效地去除硅表面中的光刻胶和有机物。此外,溶解的臭氧也可以钝化高频蚀刻后的表面,并被证明是非常有用的。
在干燥机中开发了一种原位hf最后清洗工艺,并用于预外延生长,原位清洗的结果显示,比标准的最后高频工艺有显著的改进,原位工艺对消除颗粒沉积有很大影响的原因是硅晶片没有在hf蚀刻/冲洗/干燥工艺之间穿过液体对空气的表面。本研究中进行的实验表明,使用稀释化学品和原位高频腐蚀/冲洗/干燥工艺产生的缺陷低于标准的多槽高频最后工艺,原位清洗后的缺陷与后外延生长缺陷直接相关,清洗后氧含量和颗粒缺陷越低,外延沉积缺陷越低。