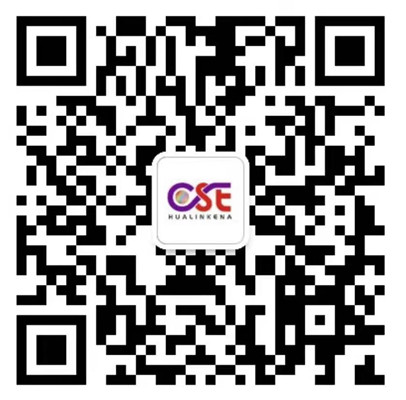
扫码添加微信,获取更多半导体相关资料
引言
绝缘体上硅(SOI)结构是低功耗和高速应用中金属氧化物半导体器件最有吸引力的候选结构之一,因为使用这种结构很容易降低耦合电容。典型厚度为几个100纳米的完全绝缘的掩埋二氧化硅层消除了几个泄漏路径。然而,许多不同的SOI结构目前正在研究中,具有标准的体结构。然而,SOI衬底是昂贵的,并且掩埋的二氧化硅的差的导热性可能产生热量问题。特定的衬底处理,如氧离子注入分离和外延层转移,必须在器件制造之前准备好。本文研究了老化时间和腐蚀时间对硅锗混合腐蚀液腐蚀速率的影响,即1 vp HF (6%)、2 vp H2O2 (30%)和3 vp CH3COOH (99.8%)。
实验
利用减压化学气相沉积系统生长了用于选择性湿法刻蚀的样品。硅衬底是在硅锗层生长之前,通过正常的清洁程序(氢烘焙步骤,以清除表面的天然氧化物,在1100℃下进行)进行清洁。然后将硅烷和GeH4(1.5%稀释)切换到反应器中,开始SiGe层的生长。硅烷和GeH4的流量分别为10~100sccm和40~300sccm。h2的流量固定在10slm。生长温度为600℃,硅锗层的生长速率为3.8纳米/分钟。最后,通过沉积40纳米硅盖层完成层结构。锗硅层中的锗浓度为20%。用透射电镜和EDX法测定了层的厚度和组成,与标称值非常一致。图1显示了通过使用RPCVD生长的Si0.8Ge0.2/Si多层的TEM图像。多层结构由10纳米厚的Si0.8Ge0.2层、40纳米厚的硅层、40纳米厚的Si0.8Ge0.2层、40纳米厚的硅层、60纳米厚的Si0.8Ge0.2层和40纳米厚的硅盖层组成。
用于蚀刻实验的样品尺寸为1 × 1 cm2,由6英寸晶圆切割而成。然后,通过使用旋转涂布机以5000 rpm旋转涂布样品30秒,用光致抗蚀剂旋转涂布样品;然后,将它们放入烘箱中,在90℃下软烤30分钟。使用掩模对准器和强度约为5 mW的紫外光(365纳米)进行光刻。具有线条特征的四英寸掩模板用于蚀刻实验的图案化。将样品浸入1∶2∶3体积(6% HF∶30% H2O 2∶99.8% CH3COOH)溶液(BPA) 。所有蚀刻实验都在室温下进行,不搅拌溶液。蚀刻后,立即在去离子水中冲洗样品30秒,然后用氮气干燥。蚀刻速率由通过扫描电子显微镜(SEM)测量的深度轮廓来确定。
结果和讨论
我们在这里考虑硅锗蚀刻溶液,即1:2:3体积(6%氟化氢/30% H2O 2/99.8% CH3COHO)溶液(BPA)。已知这种蚀刻溶液在纯硅上选择性蚀刻Si1-xGex合金。首先,讨论了不同工艺参数对Si1-xGex合金和硅刻蚀的影响。在室温下,在由双酚a组成的溶液中蚀刻Si0.8Ge0.2/Si多层。首先,准备了一种新的蚀刻溶液。在老化时间分别为0小时、24小时、48小时、72小时和96小时的蚀刻溶液中蚀刻Si0.8Ge0.2/Si多层5分钟。蚀刻速率和深度分布是根据不同蚀刻溶液的老化时间来确定的。蚀刻速率双酚a的选择性随着老化时间的延长而增加。
从硅在HF:H2O2:CH3COOH中的蚀刻速率行为观察,硅原子不容易被氧化,因为大量的HF可用于溶解任何可能形成的二氧化硅。这种行为是可以预料的,因为硅不容易被H2O2氧化。这两个平台的存在表明可能发生了两种不同的蚀刻过程。第一平台区中的蚀刻过程被认为与在HF:H2O2溶液中对Ge的标准蚀刻相同,并且由于H2O2和CH3COOH的反应而具有额外的增强。由于Ge的存在,Si1-xGex预计将在HF:h2o2溶液中蚀刻,但由于氧化Si原子的困难,应该具有较低的蚀刻速率。
然而,当使用这种水基稀释剂溶液蚀刻Si1-xGex时,蚀刻速率变低。很明显,搅拌时的蚀刻速率变化不大,因此在HF:h2o2:h2o(1:2:3)中蚀刻Si1-xGex时,没有看到蚀刻速率或等待时间对搅拌的依赖性。如前所述,这是预期的,因为硅原子存在的氧化延迟,这限制了蚀刻。在这种情况下,可用于氧化的Ge原子较少。但稀释剂醋酸的存在改变了蚀刻反应的性质。当使用醋酸代替水时,蚀刻速率是原来的两倍。
然而,他们指出,即使是容易溶的酸,如醋酸,反应也很慢,至少需要1小时才能形成。他们还指出,随着溶液中过氧化氢的量的减少,由于该反应是可逆的,因此形成的还原二氧化氢反应将被还原。这些因素可以解释过氧化氢与醋酸和Ge与醋酸之间的以下反应。
在图4中,10nm层~40nm层之间的蚀刻速率没有规律性。当Si0.8Ge0.2层厚度增加到40nm到60nm时,Si0.8Ge0.2层的蚀刻率增加。然而,当SiGe层的厚度从10nm增加到40nm时,SiGe层的蚀刻速率减小,因为发现Si0.8Ge0.2临界厚度下蚀刻速率对应变问题的影响。
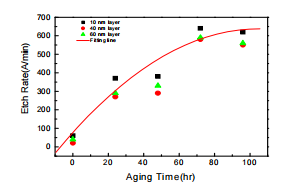
图4 Si0.8Ge0.2/Si多层蚀刻率与老化时间相比
对于湿蚀刻期间/之后的结构坍塌,在饱和老化时间后,根据不同的蚀刻时间腐蚀Si0.8Ge0.2/Si多层。图6显示了Si0.8Ge0.2/Si多层蚀刻深度轮廓的SEM图像,作为饱和老化时间后不同蚀刻时间的函数。图7显示了Si0.8Ge0.2层的蚀刻深度随饱和老化时间后蚀刻时间变化的结果。在饱和老化时,Si0.8Ge0.2层的蚀刻时间从3min增加到9min,其深度呈线性增加,如图7所示,采用饱和老化后的蚀刻溶液在蚀刻时出现坍塌。
总结
双酚a的蚀刻速率和选择性随着混合成分和使用之间的老化时间而增加。Si0.8Ge0.2层的蚀刻速率总是大于硅层的蚀刻速率,并且在72小时后的老化时间观察到硅锗层蚀刻速率的饱和。在72小时的老化时间下,Si0.8Ge0.2层和Si层的选择性为20∶1。因此,双酚a的适宜老化时间至少应为72小时。此外,蚀刻溶液的最佳老化时间应该在72小时以上,并且在9分钟的蚀刻时间出现塌陷。