在太阳能电池片制造行业中,通常单晶硅片需要进行清洗,去除各种杂质,或者利用化学品对硅片行刻蚀后形成特定的表面状态,这样才能够继续进行后续工艺生产。其中,利用碱溶液KOH进行刻蚀清洗,是一种重要的硅片处理方式。在湿法设备中集成多种化学品后,可以在单个设备上完成刻蚀、清洗等不同工艺,达到对硅片进行综合处理的目的。KOH溶液的质量分数、刻蚀时间等对硅片表面状态有重要影响。KOH刻蚀过程中需要使用大量的化学品,近年来随着技术的进步,出现了KOH碱刻蚀辅助添加剂,通过在KOH溶液中混合辅助添加剂,不仅能够达到原先的工艺要求,还能够有效减少化学品用量,降低化学品废液的处理量和难度,为今后KOH碱刻蚀大规模用提供了条件
1 实验材料和工艺
实验中,使用砂浆切割和金刚线切割的单晶硅片外观尺寸为156mm×156mm,厚度为200um,电阻率为1-3Q·cm。该单晶硅片为市场常见硅片。电池片生产工艺采用车间量产的PERC(射极纯化及背电极)单晶生产工艺。各类化学品原液质量分数如表1所示。

2 实验结果与讨论
2.1KOH预清洗
砂浆切割的硅片表面有大量的切割损伤和各种杂质等“,需要进行清洗才能开展下一步扩散工艺。通常采用KOH刻蚀的方式来对硅片进行预清洗,去除硅片表面各种脏污杂质等,达到清洗效果。清洗工艺中,通常刻蚀时间对工艺效果影响较大。实验中,保持KOH溶液质量分数18%不变,反应温度为70℃,通过改变硅片刻蚀时间,观察刻蚀后硅片的外观影响。刻蚀后硅片外观见图1.
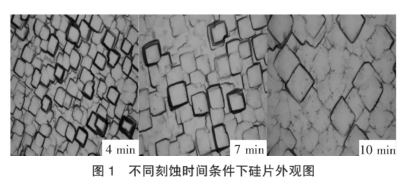
在不同的刻蚀时间下,刻蚀后硅片表面塔基底座尺寸不一样,测量尺寸如表2所示。
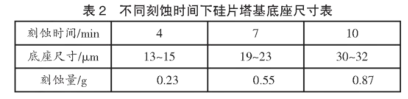
随着刻蚀时间的增加,硅片的刻蚀量逐渐增加,塔基底座的尺寸也逐步增大。通常在电池生产中,要求塔基的尺寸也逐步增大。通常在电池生产中,要求塔基的尺寸为20μm±5μm,要求保证一定的刻蚀量,从而达到清洗效果。同时,刻蚀量还不能过高,过高的刻蚀量会导致硅片变薄,后续工艺中碎片率增大,降低生产良率。不同刻蚀时间下电池片效率对比如表3所示。
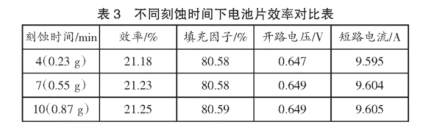
在较高刻蚀量条件下(0.55g和0.87g),电池片效率差只有0.02%,高刻蚀量(0.87g)并没有带来电池片效率的明显提升。同时,低刻蚀量(0.23g)条件下,电池片效率比0.55g条件下低0.05%,主要体现为Ua(开路电压)低0.002V.(短路电流)低0.009A,说明在低刻蚀量条件下,硅片表面的杂质和脏污并没有完全去除干净,导致硅片钝化效果较差,降低了电池片效率,证明硅片的预清洗是电池生产中的重要工艺。实验结果表明,为保证电池最终的转换效率,需要保持一定的刻蚀量(0.55g)。在车间实际生产中,为保证电池片良率,通常不采用高刻蚀量工艺生产在KOH预清洗工艺中,需要根据实验结果和生产状况选取合适的刻蚀量。
2.2清洗后硅片表面黑点
在砂浆切割硅片预清洗后检测外观时发现、在硅片表面出现了数量不一的黑点,如图2所示。不同厂商的硅片经过刻蚀后表面都出现了黑点,对比不同刻蚀时间的硅片发现,在刻蚀时间较短的情况下,黑点情况严重,出现了大量的黑点;而在刻蚀时间较长的情况下,黑点情况大为改善,数量很少。
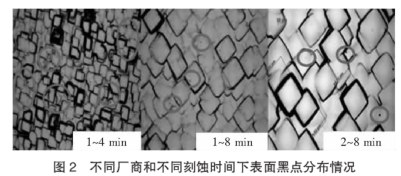
选取不同厂商金刚线切割的硅片进行短时间刻蚀,刻蚀后发现,金刚线切割单晶硅片表面基本没有发现黑点现象,见图3。
即使在较短的刻蚀时间条件下(4min),也没有出现明显的黑点残留现象。结合车间调试过程中出现的部分异常现象,进一步进行实验测试,结果如图4所示。
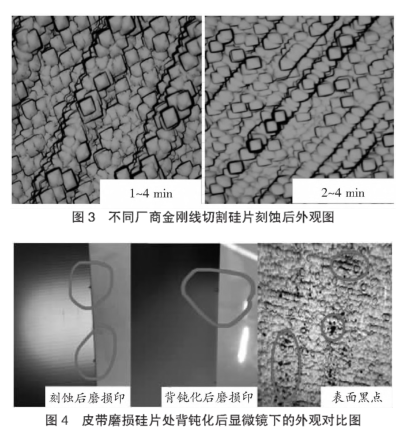
选取金刚线切割单晶硅片,在链式设备下料端,传送皮带对硅片有较严重的摩擦,外观能看到有损伤痕迹。经过背钝化工艺之后,外观磨损依然严重,肉眼可见磨损痕迹,如图4所示。显微镜放大后可以看到在磨损区域有大量的黑点,而在同一片硅片其余没有皮带损伤痕迹的位置,则没有出现黑点。通过对比可以推断,金刚线切割硅片在皮带磨损处的黑点是硅片与皮带摩擦带来的,是一种外部的污染。因此,可以推断砂浆切割单晶硅片出现的黑点是硅片在进行KOH刻蚀前带来的,并不是刻蚀工艺制程本身带来的异常。通过查阅砂浆切割硅片的工艺过程发现,该工艺主要是SiC(碳化硅)颗粒在钢线和硅片之间摩擦滚动,达到切制目的,后续经过清洗后成为成品硅片。在此过程中,硅片表面难免会残留部分SiC颗粒,因此,可以判断砂浆切割硅片表面出现的黑点为SiC颗粒。而金刚线切割硅片使用的是钢线上黏结金刚石颗粒叫,没有SiC成分,经过KOH刻蚀后,硅片外观没有出现黑点现象。
砂浆切割硅片经过长时间刻蚀后黑点减少,是因为SIC主要残留在硅片表面,经过长时间的刻蚀后,硅片刻蚀量大,表面去除层更多,因此硅片表面残留的黑点会更少可见,刻蚀清洗能够有效去除硅片表面杂质,是电池片生产中的-项重要工艺。
2.3添加剂碱刻蚀
近年来,发展出了新的刻蚀辅助添加剂方式进行刻蚀,在原有的koH配比基础上加入部分添加剂,可以大幅度减少KOH的使用量。具体配比如表4所示。
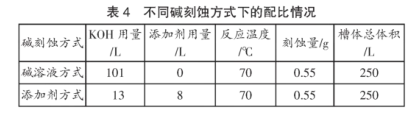
在碱溶液刻蚀方式下,要达到相同的刻蚀量(0.55g),需要在槽体中添加KOH约101L,而使用添加剂碱刻蚀方式后,KOH的用量仅仅为13L,碱用量的减少可以大大降低工业生产成本和排废处理成本。金刚线切割硅片扩散后酸刻蚀和添加剂碱刻蚀后外观对比见图5。
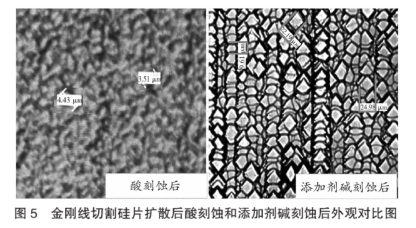
图5分别为HNO3+HF混酸处理方式(目前常用的扩散后硅片处理方式)和添加剂碱刻蚀处理方式的硅片外观图,酸刻蚀后硅片表面呈不规则外观,无明显特征,是类似颗粒状的形貌,颗粒尺寸为4~5um,而添加剂碱刻蚀后的硅片表面塔基底座尺寸与碱溶液刻蚀后基本一致,添加剂碱刻蚀方式完全可以代替碱溶液刻蚀方式。不同处理方式下硅片反射率对比见图6。

图6是硅片制绒、混酸处理和添加剂碱刻蚀后硅片反射率对比图。在同样的刻蚀量条件下,酸处理的硅片表面反射率为38%,而添加剂碱刻蚀后硅片表面的反射率较高,为46%,比酸处理方式高8%,制绒后的反射率为11%,说明在保持外观形貌和刻蚀量基本一致的条件下,添加剂碱刻蚀处理方式能够更大幅度地提高硅片反射率。不同处理方式下电池片效率她表5所示。
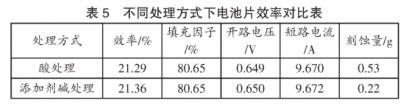
酸刻蚀和添加剂碱刻蚀处理的硅片经过后续工艺电池片效率出现明显变化。如表5所示,相较于目前常见的混酸处理方式,添加剂碱刻蚀的电池片效率更高,主要体现在U和1的提升上。添加剂碱刻蚀后,硅片反射率提高,可以使背面AI2O3更好地纯化硅片,降低电池片背面负荷,提高PERC单晶电池的转换效率[4-5]。在刻蚀碱质量对比实验中,添加剂碱刻蚀方式只需要
0.22g(酸处理方式下约41%的比例)的刻蚀量就能提高背面反射率,提高转换效率。同时,更低的刻蚀量还会降低后续工艺硅片的碎片率,在电池生产中将会有更广泛的应用。
3结语
a)随着刻蚀时间的增加,硅片减重量逐渐增大,外观塔基底座的尺寸也逐渐增大。电池片效率研究结果表明,刻蚀量对电池片效率有极大影响。在实际生产中,需要选择合适的刻蚀量对硅片进行清洗,刻蚀量过低,硅片表面未能完全清洗干净,电池片效率低;而过高的刻蚀量会导致电池片变薄,后续工艺碎片增多,降低生产良率。
b)砂浆切割的硅片表面会残留部分SiC颗粒,在清洗过程中,可以通过延长刻蚀时间来去除,但是长刻蚀时间下硅片刻蚀量增大,对后续工艺有负面影响。金刚线切割硅片经过刻蚀后则没有SiC杂质残留,从硅片洁净度角度看,金刚线切割硅片表面残留物更少,硅片洁净度更高,在生产上更具优势。
c)添加剂碱刻蚀方式下,使用少量的KOH就可以达到工艺要求的刻蚀量,在规模化生产中,不仅可以节省大量的KOH,还可以降低碱溶液废水的处理难度。添加剂碱刻独方式下PERC电池片效率比酸处理方式下高0.07%,硅片背面反射率提高,改善了电池钝化效果。同时,添加剂刻蚀方式下反射率提高后,比酸处理方式下的刻蚀量更少,硅片减薄量也更少,添加剂碱处理方式将会有更好的应用前景。免责声明:文章来源于网络,如有侵权请联系作者删除。