湿法腐蚀清洗设备是集成电路、LED、太阳能、MEMS等芯片制造中必不可少的工艺设备,而为了更好的达到腐蚀效果,在各种腐蚀工艺中往往要配合药液的循环完成,从而达到更好的腐蚀均匀性。华林科纳(江苏)半导体CSE工程师介绍了几种常用的腐蚀工艺循环原理及在湿法腐蚀清洗设备的典型应用。
关键词:工艺槽循环过滤; 湿法腐蚀清洗; 硅腐蚀;
随着芯片制造特征尺寸的缩小,工艺水平的不断提高,对晶片腐蚀的均匀性,晶片表面颗粒及金属污染等洁净度指标提出了更高的要求,因此,湿法腐蚀清洗设备在采用晶片旋转、抖动、超声清洗、兆声清洗等的同时,业内普遍采用工艺槽循环过滤方式,来净化槽内药液,同时均匀流场保证药液浓度和温度的均匀性。
1 湿法腐蚀的关键问题
硅的湿法腐蚀在选择腐蚀工艺和腐蚀剂时,需考虑诸多因素影响(如浓度、时间、温度、搅拌等)的同时,需考虑以下几方面的问题:
(1)腐蚀速率。较高的腐蚀速率将有效的缩短腐蚀时间,但所得到的腐蚀表面较粗糙。腐蚀液的浓度与腐蚀速率及腐蚀表面质量有关,当腐蚀液浓度较小时,腐蚀速率较大。
(2)腐蚀选择性。选择性是指要腐蚀材料的腐蚀速率与不希望腐蚀的材料(如掩模)的腐蚀速率的比率。一般地,选择比越大越好。
(3)腐蚀均匀性。在硅腐蚀表面各处,腐蚀速率常常不相等,造成腐蚀表面出现起伏等,腐蚀尺寸比较大时表现尤为明显。这与腐蚀液浓度有关,反应槽中腐蚀液的浓度一直在变,并且各处浓度难保持一致性。因此,有时在腐蚀过程中一直伴随着均匀搅拌,这将有效地保持腐蚀液浓度的均匀性。
(4)腐蚀表面粗糙度。不同的腐蚀方法和腐蚀剂将得到不同程度的表面粗糙度,它与腐蚀液、腐蚀速率等密切相关,与温度关系不大,但温度升高会导致腐蚀速率的增大。湿法腐蚀清洗设备使用的化学药液很多,有酸性腐蚀剂,碱性腐蚀剂以及有机腐蚀剂等,这些化学药液通常具有较强的腐蚀性,特别是有机药液还具有易燃、易爆特性,同时它们的使用温度也不尽相同,有常温也有高温,依据不同的药液,以及不同的工艺要求,我们在循环管路的设计上也有所不同。主循环回路大体由储酸槽,泵,加热器,热交换器,过滤器,传感器(压力、温度、流 量控制) 等,供酸和排液的药液阀及废液回收管道组成。下面就总结一下常见的湿法腐蚀清洗设备中循环管路的应用。
2 湿法腐蚀工艺中循环管路的应用
2.1 硅腐蚀工艺
硅腐蚀工艺一般有酸腐蚀和碱腐蚀两种。硅酸腐蚀通常使用 HF-HNO3 或 用 HF-HNO3-HAc(CH3-COOH,醋酸)的混合酸。硅腐蚀根据工艺的不同,腐蚀温度也有所不同,范围为 -15°~20°不等。所用到的槽体材质一般为 PVDF 材质。
反应式如下:
Si + 4HNO3→ SiO2→ 4NO2 + 2H2O
SiO2 + 6HF → H2SiF6 + 2H2O
醋酸是一种控制腐蚀速度的酸,当混合比率大时,腐蚀速度就减小,而且会影响硅中的杂质浓度。由于反应温度的关系,一般我们要在工艺槽的循环管路中接入制冷机、热交换器,从而使药液温度达到所需的低温度要求。除此之外,管路中还需接入磁力泵来提供药液的循环动力。因此药液的循环:由磁力泵、循环溢流槽、制冷机、热交换器、流量计、管件等组成药液的循环过滤系统。实现药液的循环,保证工艺槽药液温度和浓度的均匀性。
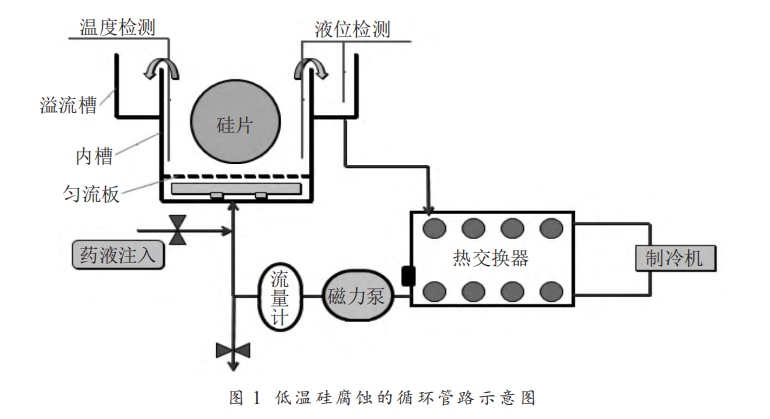
图 1 是低温硅腐蚀的循环管路示意图。
硅腐蚀工艺中另一种腐蚀即为碱腐蚀,其所用到的药液一般为 NAOH 或 TMAH(四甲基氢氧化铵),工艺温度一般为 90℃。对此我们在工艺槽体内直接用投入式加热器来对药液进行加热达到工艺温度或采用在线加热方式。除此之外,管路中还需接入风囊泵来提供药液的循环动力。因此药液的循环由风囊泵、循环溢流槽、投入式加热器或者在线加热器、阀门、管件等组成药液的循环系
统。实现药液的循环,均匀流场。保证工艺槽药液温度和浓度的均匀性。槽体材质一般采用 PTFE材质。图 2、图 3 是高温硅腐蚀投入式加热和在线加热的循环管路示意图。
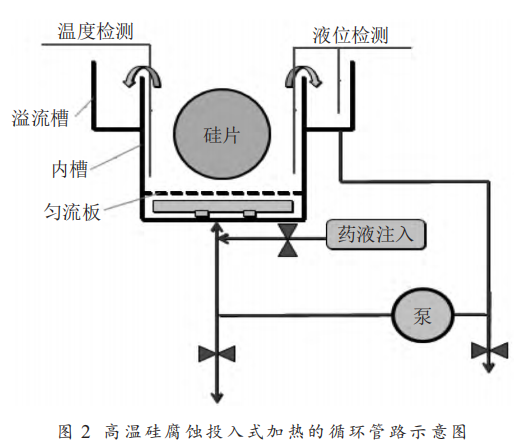
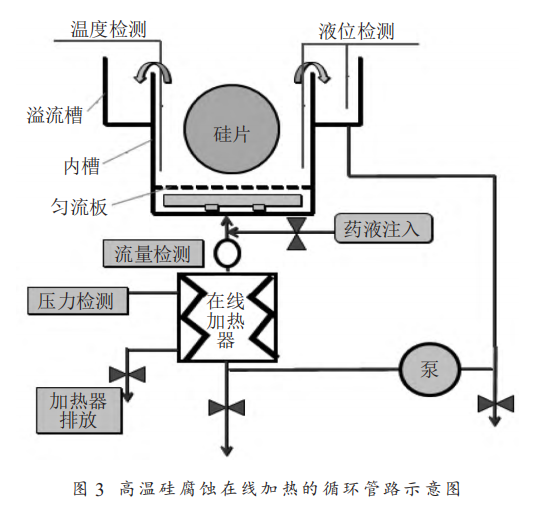
2.2 二氧化硅腐蚀工艺
SiO2 的腐蚀是用 HF 来实现的。药液一般有BOE、HF、DHF 等。由于腐蚀速度快,因而均使用NH4F(氟化铵)作为缓冲剂来减慢腐蚀速度。普通叫做缓冲腐蚀。此种工艺在常温下进行,而根据我国南北方生产的需要为了维持常温,在北方,往往要配合小功率(200~300 W)的投入式加热器,以防止反应结晶;而在南方则需加入冷却盘管,以适当控制温度。一般工艺槽体材质选用 PVDF 材质。
除此之外,管路中还需接入泵来提供药液的循环动力。由于隔膜泵在连续不间断工作时膜片使用寿命较短,更换膜片较频繁,目前这种应用方式逐渐被风囊泵所取代。因此药液的循环过滤:由风囊泵、过滤器、循环溢流槽、阀门、管件等组成药液的循环系统。实现药液的循环过滤,均匀流场。保证工艺槽药液温度和浓度的均匀性。
图 4 是二氧化硅腐蚀的循环管路示意图。
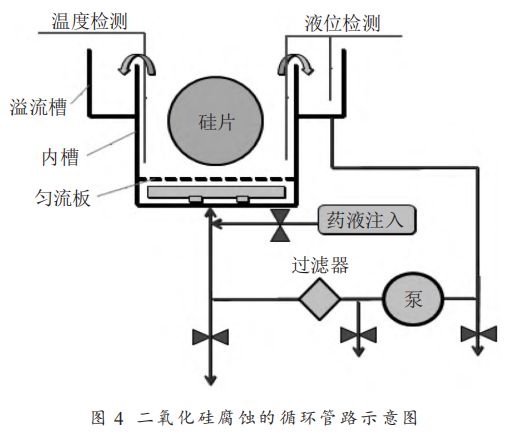
2.3 铝腐蚀工艺
对于 Al 腐蚀来说,碱和酸都能用来腐蚀它,但半导体技术中所使用的腐蚀液使用磷酸系物质作腐蚀剂较多一些。例如 H3PO4-HNO3-HAc-H2O 铝在磷酸中几乎不被腐蚀,但当混入 HNO3 时,腐蚀速度才快。使用的混合比率尽管多种多样,然而如在 H3PO4∶HNO3∶HAC∶H2O=15∶1∶2∶1 场合下,能够得到约 0.1 μm/min 的腐蚀速度。当在 Al中掺有硅时,腐蚀速度可提高到 1.2~1.5 倍。
而根据工艺条件的不同,我们又可以将铝腐蚀分为真空铝腐蚀和非真空铝腐蚀两种。真空铝腐蚀,即在抽真空的条件下,在药液槽中进行腐蚀,工艺温度为 52℃,工艺槽材质选用 不锈钢材质,不同于其他腐蚀工艺的是此工艺槽只循环无溢流,加热方式采取贴膜加热,泵体的选择为真空泵,即水环泵。因真空条件要求,槽体需要密封设计。
图 5 是真空铝腐蚀的循环管路示意图。

非真空铝腐蚀,是相对于真空铝腐蚀而言。工艺温度一般为 60℃,工艺槽材质选用 PVDF 材质,加热方式采取投入式加热。除此之外,管路中还需接入风囊泵来提供药液的循环动力。因此药液的循环过滤:由真空泵、循环槽、阀门、管件等组成药液的循环系统。实现药液的循环过滤,均匀流场。保证工艺槽药液温度和浓度的均匀性。
图 6 是非真空铝腐蚀的循环管路示意图。
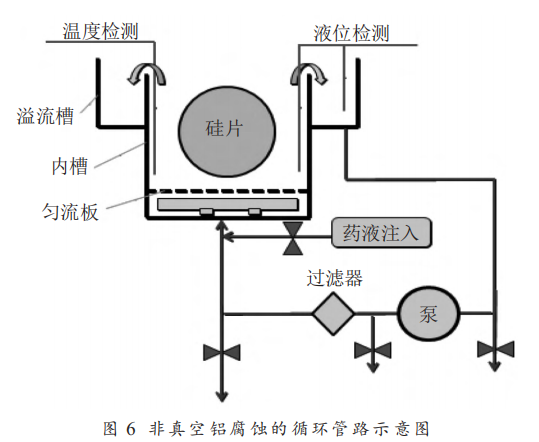
近几年来,伴随着硅片的大直径化,器件结构的超微小化、高集成化,对硅片的洁净程度、表面的化学态、微粗糙度、氧化膜厚度等表面状态的要求越来越高,硅片的各种腐蚀技术都在不断的发展,华林科纳(江苏)半导体设备公司CSE也对硅片的腐蚀效果及均匀性提出了更高的要求,对于工艺槽体管路的研究以及器件的选择有着很重要的意义。