LED 芯片是一种将直接电能转化为光能的半导体器件,是现代信息产业的核心器件。随着我国科学技术的不断进步与微电子设备研制的发展,国内从事芯片设计制造企业也逐渐增长到几百家,但是他们普遍自主知识产权及自主创新设计制造水平不高。LED 芯片制造及高端
封装技术是技术密集型产业,其发展水平离不开高端工艺与硬件设备。近年来国内微电子设备产业急速扩张,而支撑其技术引领的高端设备却严重缺乏,发展瓶颈逐渐成形。目前产业高端设备依然依赖国外进口,亟需开发研制自己的高端设备。
LED 封装就是在保证其芯片无损以及高光取出效率的前提下将外部引线与内部芯片电极相互连接。在整个LED 产业链当中,封装技术是产业与市场的连接纽带,而在 LED 芯片制造和高端封装过程当中去胶这一工艺过程起着非常重要的作用。
1 当前面向 LED 芯片制造和封装去胶设备现状
随着科学技术水平的不断发展,集成电路技术现已主要通过凸点封装模式来大幅提升封装密度与效率。凸点封装技术包括了膜沉积、光照、去胶等多项半导体芯片制备技术。现代高端封装工艺一般面向 300 mm 晶圆、65 nm 及以下极大规模集成电路封装需求,开发凸点个数3000 以上、间距 200 μm 以内的小间距凸点制作技术和再布线技术。其核心过程是在已制成芯片的特征位置定义并形成凸点、重布层(RDL)或通孔(Via)等特征图形。由于特征尺寸的缩小、特征图形密度的增加,其特征图形的定义就必须通过涂覆超厚胶 膜 、光刻、显影、去胶等工艺制程来实现。
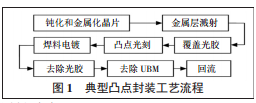
图 1 为典型凸点封装工艺流程图,其中光刻胶膜较厚,通常会达到 50~100 μm。由于电镀产生的凸点一般会有类似蘑菇头的结构,当凸点密度较大时,采用传统槽式去胶,其根部的光刻胶不易去除干净,会影响后续的UBM 刻蚀,造成回流后凸点高度的不一致。因此急需开发一种高密度凸点封装工艺中所必须的全自动去胶机。
目前半导体 IC 封装的主要发展趋势为多引脚、窄间距、小型、薄型、高能、多功能、高可靠性和低成本,对系统集成的要求越来越迫切,三维集成封装技术由此应运而生。三维集成封装的两种最通用技术是通过传统打线结合结构的使用,以及通过穿硅通孔(TSV)技术建立芯片叠层的元件之间的电子连接性。然而,当 I/O 个数和叠层数量增加的时候,打线接合已经不实用。利用TSV 技术实现芯片间的垂直通孔,从而达到最大的堆叠密度和最小空间尺寸。TSV 技术已经在逻辑线路、存储器、CMOS 图像传感器(CIS)等产品的封装技术中得到部分应用,TSV在三维集成封装制造过程中已经变得越来越迫切。
相对于传统凸点封装,3D-TSV 工艺对新型光刻胶喷涂机、圆片键合机、硅片减薄机、TSV 等离子刻蚀机和双面光刻机提出了新的需求。目前国内 LED 芯片和封装生产企业所采用的去胶设备均为手动或半自动去胶槽,化学液消耗量较大,工艺参数不易控制,结果重复性差。
在高端封装和 LED 工艺中,光刻胶膜一般较厚,通过开发面向 LED 芯片制造和高端封装旋转式去胶机,实现高压喷射去胶液或常压喷洒去胶液,结合兆声波的方法快速干净地去除光刻厚胶。因此研制满足 LED 芯片制造和高端封装(如:BGA、MCM、WLP、3D-TSV 等)生产需要的全自动湿法去胶设备(简称去胶机)尤为重要。同时,该设备与双面光刻机、通孔(TSV)刻蚀机、圆片减薄机、高密度倒装机、电镀机、硅片清洗机等联线,组成高密度封装和LED成套工艺设备,可以促进当前高端封装技术发展。
2 旋转式去胶机的设计
2.1 布局设计
通过对满足 LED 芯片制造和高端封装生产需要的自动湿法去胶设备的研制,实现该设备与双面光刻机、通孔(TSV)刻蚀机、圆片减薄机、高密度倒装机、电镀机、硅片清洗机等联线,组成 高 密 度 封 装 和LED成套工艺设备。整个 设 备 的 布局如图 2 所示,主要有电控单元、化学液供应单元和反应腔体单元,其技术开发的核心是反应腔体的设计。
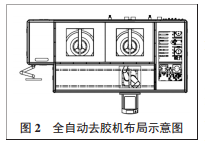
2.2 反应腔体单元结构设计
全自动旋转去胶机的反应腔体主要由三大部分组成:摆臂系统、夹持系统和回收腔。其中,摆臂系统主要完成反应腔体化学液体、氮气以及水的传送,在该系统中所有反应物质通过该系统实现在清洗目标硅片上的均匀分布,提高去胶效果;夹持系统主要完成去胶硅片的夹持工作,在夹持硅片的过程中利用气压传动技术实现其高速旋转,同时保证硅片正面清洁无污染,为提高去胶效果,该系统还可以同时完成直线上下和旋转运动;回收腔主要完成化学液和水的回收,为提高化学液的利用效率实现循环利用,回收腔采用分层设计,不同的化学液体将在回收腔中实现分类回收。
该反应腔体结构示意图如图 3 所示。该反应腔体在摇摆送液手臂以及其他装置的作用下,可以完成不同种类化学去胶以及水洗清洁干燥等自动化同时进行,实现良好的去胶效果。该装置工作时,首先会将通过夹持装置将目标硅片锁定在腔体的底层,通过摆臂系统均匀将一种化学液喷洒在硅片上,并完成去胶和回收;再通过夹持装置将硅片提升至图 3 所示位置,摆臂系统再次输送其他化学液,完成去胶和废液回收;最后直至光刻胶去除完全后,硅片在夹持系统作用下升至顶部,完成水洗、干燥和废液回收,完成整个去胶工序。
2.3 主要技术指标及效益
通过对面向 LED 芯片制造和高端封装旋转式去胶机的设计与研究,设备达到如下指标:1)晶片尺寸:准200~300 mm;
2)去胶腔体:2~4 个;
3)去胶方式:全自动单片旋转湿法喷淋式、化学液高压喷射和兆声波;
4)去除胶层:5 ~50 μm 正胶、50 ~120 μm 负胶;
5)去 胶 化 学 液 :含DMSO、NMP 等各种去胶液;
6)去胶液温度:25~80 ℃,1 ℃;
7)去胶速率:10~20μm/min以上;
8)颗粒去除:0.5μm颗粒 95%以上。
市场需求不断提高,生产工艺技术不断改进等外、内部因素无不促使面向 LED 芯片制造和高端封去胶设备需不断进步,这样才能在涉及半导体、光通信、PCB 等领域充分满足不同客户的需求。
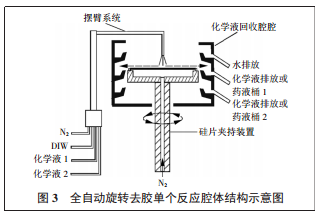
3 结 论
面向 LED 芯片制造和高端封装旋转式去胶机的设计与研究可以对当前封装领域去胶设备有效补充,同时该设备研究可以实现快速去除厚度在 50~120 μm 的厚感光胶膜;清洗 Bump 根部和3D-TSV 深孔底部的光刻胶残留;单片去胶时,硅片正面喷洒化学液,有效地保护硅片的背面不被化学液污染;有效设计反应胶,通过进风与排风的有效配合,使整个腔体内部流动的气体形成层流,从而带走去胶过程所形成的水气和溅射出的光刻胶,避免硅片表面的二次污染;新型化学液供应系统,在化学液喷洒过程中保持稳定的工作温度,尤其是在某些制程需要高温化学液(如 70 ℃);能够回收喷洒后的化学液,在线去除化学液中的光刻胶残留,循环使用化学液,节约成本等显著特点,具有十分重要的现实应用价值。
更多的半导体材料工艺设备相关资讯可以关注华林科纳CSE网站:
www.hlkncse.com,现在热线咨询400-8768-096,可立即获得免费的半导体清洗解决方案。