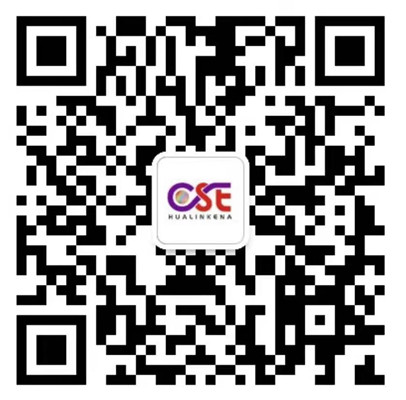
扫码添加微信,获取更多半导体相关资料
介绍
随着超大规模集成电路器件制造过程中封装密度的增加。可接受的金属 污染水平的要求变得更加严格。因为痕量的金属杂质影响电子器件的 性能;所以需要高度精确的分析技术。
VPD制剂已经与几种不同的痕量元素分析技术相结合,例如 电感耦合等离子体质谱(ICP-MS)、47原子吸收光谱法(AAS)和全反射 X射线荧为了分析大块硅晶片中的金属杂质,使用蚀刻或大块分解样品制备 。15, 16整个晶片表面被蚀刻至一定深度,或者硅样品被酸分解。
然后是 分解的硅和酸通过在热的盘子。通过分析仪器測量去除基质后残留的金属杂质。这些方法的 结果,例如VPD制备、蚀刻或整体分解,显示为整个晶片表面或整 体的平均值。然而,在器件或晶片制造过程中,金属杂质不会均匀 地污染晶片。
程序
晶片被放置在主板和盖板之间。将采样管放在特定位置的孔 中进行分析。将100微升蚀刻溶液滴到被采样管包围的晶片 表面上° —根真空管连接在采样管的孔中。通过真空泵排出 反应气体,并通过在晶片下点亮红外线灯来干燥蚀刻溶液。在干燥蚀刻溶液后,移除盖板和真空管。
结果和讨论
局部蚀刻条件的优化
蚀刻溶液被固定为HF和HN。的混合物:在半导体工业中,它已经被用作硅的蚀 刻溶液很昧时间孑。蚀刻溶液的体枳被限制在10暗升注以避免蚀刻反应过程 中化学物质的任何泄漏,以及当使用大体积时去除溶液所需的长干燥时间。期 望的蚀刻深度是10 umo 一个装置
图案通常在距离硅晶片表面10 um的深度内制作。因此。我 们一直在关注这个深度的金属杂质。表2显示了由不同组成 的蚀刻溶液(HF: 2%、5%和10%)产生的硅晶片的蚀刻深度当HF的浓度为5%时,获得10 um的蚀刻深度。
局部蚀刻程序的恢复测试
在最佳蚀刻条件下进行了回收试验。在本实验中获得的检测 限也给出了条件。表3中的100微升L0纳克/毫升-1标准品。 将铁、铜和镣的标准溶液移至空白溶液的水表面偏差上,用, 相同的溶液处理并通过红外线灯干燥,使用三倍的标准溶液I 计算它们。包含污染程序的区域,没有尖峰。用局部蚀刻技 术分析斑点。回收率被确定为测量浓度与初始污染浓度之比' o如表3所示,从五个样品的平均值获得95-112%的回收率。
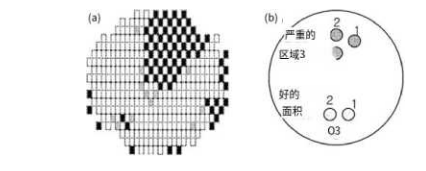
图3 铜污染晶片的BV失效分布
真实样本中的应用
将这种局部蚀刻技术应用于镣和铜污染的晶片,用于硅晶片 的吸杂研究。在这项研究中,将少量的铜和镣污染物溶液滴 到晶片表面的任意位置,并进行热处理以扩散到晶片体。晶 片上的污染位置和使用局部蚀刻技术的测量结果如图2所示 o A和D位置分别被500微升1微克毫升-1的铜和線污染。B区 和C区没有被污染构图,并测量氧化物击穿电压。在图3中,电不良区. 域和电良好区域被区分为黑色和白色矩形o BV失效的: 标准是8MV/cm。最终,BV结果显示了失败分布中的 特定区域趋势。与其他区域相比,晶圆图的上侧区域. 出现了更大的BV故障。据推测,表面条件将沿着晶片 的浸渍方向变化。