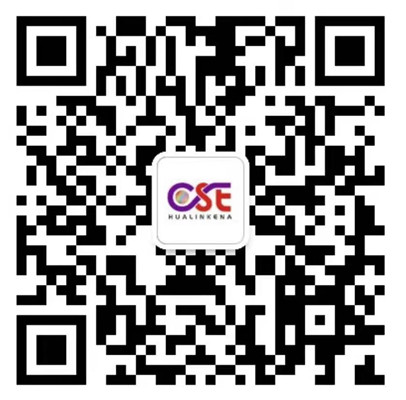
扫码添加微信,获取更多半导体相关资料
引言
硅是一种具有许多特殊分子性质的材料,可以作为许多化学器件的重要候选材料,如传感系统和锂离子电池的阳极材料。然而,由于硅的低表面积,它并不被认为是适合许多设备的材料。另一方面,多孔硅由于其独特的表面、电学和光学性能,目前是一种非常适用的材料。一般来说,多孔材料根据孔径分为三类:大孔(大小在50nm以上)、中孔(50-2nm)和微孔(小于2nm)。近年来,中孔PSi的合成因其对从光电子学到电化学电源等一系列器件的良好制造特性而受到越来越多的关注。在本研究中,我们研究了多孔硅样品在各种电化学蚀刻条件下的形态特征的变化,如电解质组成和浓度、应用电流密度和蚀刻时间。用场发射扫描电子显微镜和扫描电子显微镜观察了其形态学特性,并与蚀刻参数相关。
实验
首先,通过化学抛光制备了掺硼型单晶硅片。这些晶圆用所谓的RCA方法进行化学抛光。这些晶片随后被氮气干燥。然后,将硅晶片切成1×1Cm2片。另外,在低电阻率样品的1×1Cm2片的背面涂覆了一个500nm的铝薄膜,提高了蚀刻电流密度的均匀性。测量到的硅基板电阻率范围为0.01Ω。Cm~12Ω。Cm。通过RCA清洗的硅基底电化学蚀刻制备多孔硅样品。两种组分溶液的电解质由HF、乙醇和去离子水组成。电化学蚀刻是在10mA/Cm2~50mA/Cm2范围内进行的电化学蚀刻。蚀刻时间从5分钟到30分钟不等。电化学蚀刻电池由一个如图1所示的聚四氟乙烯壁容器组成。蚀刻后的样品在蚀刻后用薄片组织干燥。
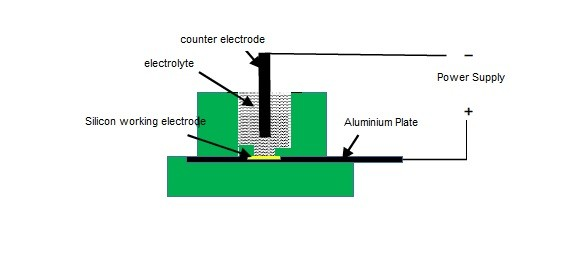
图1电化学蚀刻电池的示意图表示
结果和讨论
图2显示了电化学蚀刻在HF:乙醇溶液中以1:5、1:4和1:3比制备的多孔硅的S电镜图像。硅样品的电阻范围在8Ω。Cm~12Ω。Cm之间,导致硅的宏观孔隙度。图2-a描绘了一个均匀的平面,由于成分比(1:5)和低电流密度,它没有被完全蚀刻。低浓度的HF导致了少量的多孔层,而我们的扫描电镜显微镜无法检测到。图2-b显示了采用较高的HF体积比(1:4)制备的样品的海绵状微米孔隙。如果电流密度和HF组成比同时增加,则海绵状形态将被破坏,如图2-c所示。
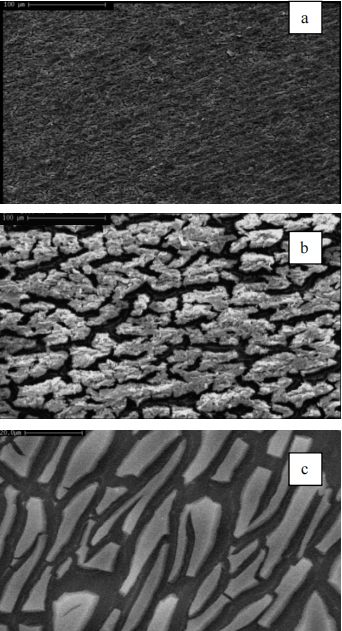
图 2
在电化学蚀刻过程中,电流密度对中多孔硅样品的孔隙宽度有重要影响。图4-a-4-d显示了不同电流密度的多孔硅样品和人的FESEM显微图。HF/乙酯的相同化学比例为1:3。将电流密度从10mA/Cm2增加到40mA/Cm2,导致孔径分别从图4-a中的9nm增加到图4-c中的23nm。结果表明,随着孔径的增大,初始小孔隙与一个大孔隙合并,比表面积减小,以及早期孔隙壁的破碎,导致更大的孔隙形成。另一方面,电流密度的值决定了硅与电解质界面层发生电化学蚀刻反应的速率。外加电流密度的数量越高,初始凹坑宽度越宽,导致大孔自组装。
刻蚀时间的增加会导致电解质对深层硅层的腐蚀,并有足够的时间与衬底反应。图3描述了在前层后面观察到的中孔硅内部层的情况。似乎蚀刻时间的增加导致孔隙深度的增加,而施加电流密度的增加导致孔隙宽度的增加。
结论
结果表明,多孔硅的形貌与蚀刻参数极为相关。不同的电流密度导致不同的孔隙大小,而蚀刻时间导致不同的孔隙深度。两分量溶液的孔隙尺寸随电流密度的增加而单调增大,三分量溶液的孔隙尺寸呈指数增大。这种通过控制蚀刻参数的自组装电化学工艺引起的调谐工艺适用于多孔薄膜的制备。