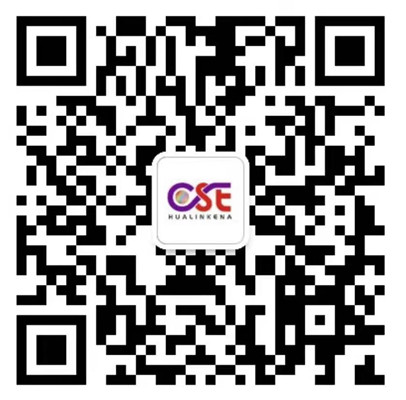
扫码添加微信,获取更多半导体相关资料
本文提出了一个利用基本物理机制的数学模型,并提供了一个全面的过程模拟器。该模型包括流体流动、静电效应以及体积和表面的相互作用,应用于研究基于高频的高k微纳米结构的图案晶圆冲洗动力学的具体案例,研究了水流、晶圆旋转速率、水温、晶圆尺寸、晶槽位置等关键冲洗工艺参数的影响。
图1
冲洗过程中旋转晶圆表面的流体流动模式示意图如图所示1a。在晶片中心引入的冲洗水从中心向边缘流过晶片表面,水膜的形状围绕z轴是对称的,该沟槽如图所示1b,表示微观或纳米结构,晶片上的冲洗水层由两个区域组成:待清洗的沟槽内以及在旋转晶片上形成的薄膜内。
杂质冲洗和去除过程中涉及的各个步骤受到基板壁表面电荷的影响,该电荷受到晶片表面附近边界层的成分的影响,开发单晶圆旋转漂洗工具过程模型所涉及的关键配置和操作参数是旋转速度、水流、水温、晶片尺寸、特征尺寸和初始污染物浓度,本研究中的污染物为1%的氢氟酸,该模型考虑了漂洗过程的细节,包括液相和高温高k表面的化学反应,以及电场下的扩散、对流和迁移,模型参数,如表面相互作用速率系数和扩散系数,取决于杂质的类型和表面的化学性质。
对表面充电会导致微纳米结构表面附近形成静电场,这种静电场会影响到沟槽内离子的分布,随着沟槽尺寸的减小,在沟槽表面附近形成的德拜层变得更加重要,并影响了沟槽内离子的输运,这个德拜层的厚度与离子种类的浓度成反比,因此在液体(水)中的污染物离子浓度较低时变得越来越重要。
在表面制备过程中,化学物质存在于液相和沟槽表面,液相中发生的各种反应,有必要考虑表面反应,以全面了解冲洗过程。假设氟离子不优先吸附在所有带电的表面位置,因此,吸附和解吸的速率取决于离子种类与带电表面之间的相互作用力,利用石英晶体微平衡对氧化铁随时间的变化进行拟合,确定模型的关键动力学参数吸附、解吸和蚀刻速率系数。
为了验证工艺模型,我们进行了特殊的冲洗实验,首先将带有图案的氧化铁膜表面层的晶片暴露在高频溶液中清洗,然后用超纯水冲洗。晶片图案包括用于冲洗监测的ECRS通道。利用传感器阻抗测量能力监测传感器通道中剩余高频的冲洗情况,实验数据与1:100(HF:H2O)稀释氢氟酸溶液以800rpm转速和1.2l/min流量冲洗模型预测的比较,显示了4米宽、2米深的微通道内溶液的阻抗。
图中所示的浓度是位于晶片边缘的沟槽的拐角,结果表明,随着自旋速率的增加,漂洗效率开始增加,然而,增加旋转速率超过800rpm没有进一步影响冲洗效率。在这些实验中,水流速在0.3l/min到8l/min之间变化,而转速保持在800rpm不变,结果表明,随着流量从0.3l/min增加到4l/min,吹扫状态的持续时间逐渐减小,当流量高于4l/min时,流量的影响不显著,在低流速下,化学传输速度较慢;因此,高流速会导致更快地清除靠近晶圆表面的液体层中的污染物。
已经证明,在冲洗过程中,更高的流速和更高的旋转速度将有助于达到所需的清洁水平。然而,超过最佳旋转速度和流量,有益效果变得不显著,这种减少的好处是由于旋转速度和流量对微观结构的内表面和晶圆表面附近的边界层的污染物的去除没有太大的影响,观察这些最佳条件对于避免不必要的能量和水的浪费以及处理时间是很重要的。
利用实验结果和过程模拟相结合,开发了新的分段冲洗策略和配方,可以降低水和能源的使用,改善整个工艺,在800rpm下冲洗300mm氧化硬膜晶片,将传统的冲洗方法与已开发的分阶段冲洗方法进行了比较,由于较高的电荷密度和德拜层从两个方向上的延伸,沟槽角落的电场比沟槽中心延伸得更远,当表面和残留物有相反的电荷时,这种大的电场使清洗变得困难。
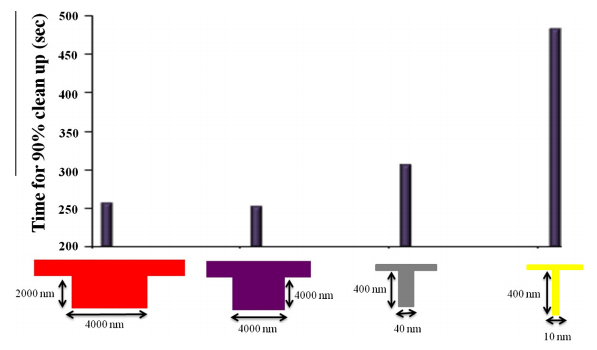
图10
图10显示了不同特征设计中不同沟槽角落处90%清理表面残留物所需的时间,结果表明,冲洗时间随特征尺寸的长宽比的增加或沟槽宽度的减小而增大,这表明,随着制造从微尺度转移到纳米尺度,纳米结构的清洗变得更具挑战性,并将涉及到显著增加资源的使用。
最后建立了一种研究单晶圆旋转冲洗工具中冲洗和清洗动态的综合过程模型,并将其应用于火腿基图案基板的冲洗,该过程模拟器考虑了离子的吸附、解吸、对流、扩散、迁移和表面电荷,研究了水流、晶片旋转速率、水温、晶片尺寸和沟槽位置等关键冲洗工艺参数对晶片的影响,结果表明,较高的水流和较高的晶圆纺丝有助于冲洗工艺。
然而,有一个最佳的流量和旋转速度,超过这个速度,对冲洗过程的好处变得微不足道,分期冲洗方法可用于优化冲洗过程,减少水和能耗,提高吞吐量,结果表明,与传统的300mm晶片尺寸的漂洗配方相比,通过使用分段漂洗配方,用水量降低了74%。对沟槽位置和晶片尺寸的影响的结果表明,位于晶圆边缘的沟槽比位于晶圆中心附近的沟槽更难清洗,而且随着沟槽宽度的减小,清理时间也显著增加。此外,晶圆越大,清洗有图案的晶圆所需要的时间就越长,本研究开发的工艺模拟器是提高清洁性能、降低水和能源使用、降低成本的有力工具。