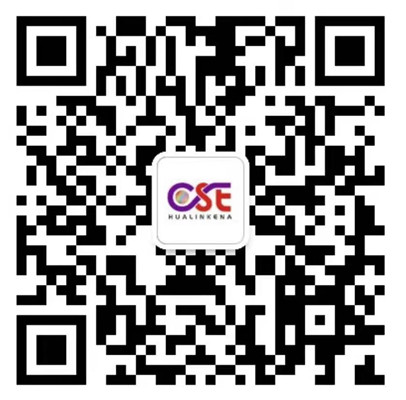
扫码添加微信,获取更多半导体相关资料
本研究利用大气等离子体,以等离子体表面处理取代化学辅助有机清洗工艺,减少三氯乙烯和氢氧化钠等化学物质的使用。通过采用大气等离子体处理,在不使用危险化学品的情况下,获得勉强可接受的电镀和清洁结果,实验结果表明,从环境友好的角度来看,用等离子体处理代替化学过程是合理的,此外,还对浸锡/铜进行了等离子体处理,以了解等离子体处理的锡/铜的可焊性,用于实际工业应用。
本实验采用的MyPLTM最大直列可处理300 mm的电路板尺寸,适用于大体积微电子封装制造环境,该系统由射频电源系统、气体输送系统和等离子体产生系统三部分组成,射频电源系统采用13.56兆赫射频电源,带有自动阻抗匹配模块,气体输送系统有四个带数字控制系统的质量流量控制器。
图1
实验的起点是通过扫描电镜图像比较镀铜样品,扫描电镜图像是通过常规化学清洗和等离子清洗从样品中获得的,将两个铜箔样品用水清洗,用化学试剂和等离子体有机清洗,用H2SO4酸洗,并用硫酸铜4H20对清洗后的铜样品进行电镀。图1显示了电镀后的扫描电镜图像,但是不清楚哪种清洗方法优于另一种,似乎图1(b)是等离子体清洁的样品,显示了局部形成的稍大的铜颗粒,但是图1(a)显示了更均匀的表面。通过扫描电镜图像观察清洁效果可能会导致表面的近视,因此在以下实验中选择了更宽的观察视野。
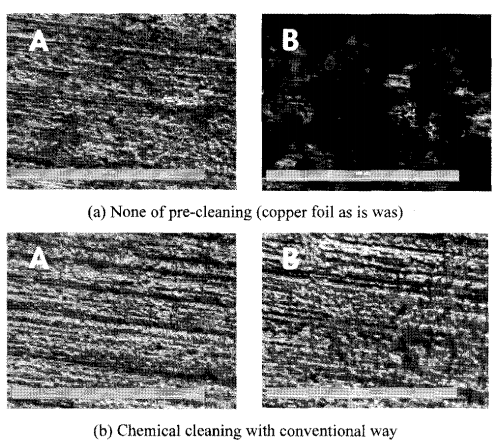
图2
化学清洗是通过将样品浸入化学物质如三氯乙烯、氢氧化钠和硫酸中三分钟来完成的。对于等离子体清洗,供应10、20和30 sccm的氧气,同时输送10 Ipm的氩气载气,这个实验的显微图像如图 2,在图2(a)中,呈现了没有任何预清洗的铜箔样品,图A分别显示了最清洁的区域(或残留区域)和图B显示了污染最严重的区域(或未清洁区域)。样品的某些区域足够干净,可能不需要有机清洗,然而,在一些区域,非常暗的斑点被有机材料污染,在电镀铜之前应该清洗。图2(b)显示了通过将样品浸入指定的化学浴中三分钟,用三氯乙烯和氢氧化钠预清洗的样品,这些样品看起来很干净,没有任何深色污染点。
在氧为30 sccm的情况下,离子化的氧可能分解样品上的有机成分,但高能氧等离子体也能与表面的铜离子反应形成氧化铜,从等离子体处理的实验结果来看,大约20 sccm的氧气给出了与化学清洁表面相当的清洁效果,并且用等离子体清洁代替化学清洁的假设在某种程度上是可行的,这表明氧等离子体有利于金属表面的有机去除,但可能需要长时间的酸洗才能在铜表面进行微蚀刻。
为了防止铜在元件封装或印刷电路板制造中被氧化,铜金属化上的浸锡涂层是最终制造过程中的常用工艺,并且它可以被安全地储存用于下一个组装过程,在互连金属等离子体表面处理的第二阶段,我们对浸没的锡/铜表面进行了氦/氩等离子体处理,通过用锡表面的离子键取代悬挂键来保护锡免受氧化。
为了比较等离子体处理的效果,将制备的样品分成两组:一组不进行等离子体处理,另一组进行等离子体处理,在300瓦射频功率下,用5 %氦/氩混合气体对锡/铜薄膜进行大气等离子体处理,使用XPS进行表面分析有助于揭示等离子体表面处理的效果,但我们已经通过测量润湿力对锡表面进行了可焊性测试,以便进行工业应用。
本实验中的多次回流测试对于模拟实际使用的实际装配过程是合理的,回流前的润湿力与未处理的样品相同,在假设中,表面的悬空键变成了与等离子体离子的离子键,这可能会降低表面氧化的概率,然而,在多次回流时观察到一个有趣的润湿力测量,结果表明润湿力随着回流时间的增加和达到最大润湿力的时间的增加而降低,这对于开发新的工艺是一个令人惊讶和非常不满意的结果,因为可焊性性能比未处理的样品差。
为了理解多次回流时可焊性差的机理,还对锡和铜之间形成的金属间化合物进行了顺序电化学还原分析,没有回流的两个样品显示出相似的IMC结构,因此以相似的方式记录润湿力,在回流工艺之后,两个样品的IMC结构显示出差异,在经等离子体处理的样品中,n层中间相的厚度相对于未经等离子体处理的样品有所减少。这背后的原因尚未明确,但据认为锡铜结合较少,所以金属间化合物的厚度呈现出不同的模式,这与铜表面处理的情况类似,但我们没有预料到多次回流工艺后等离子体处理样品的可焊性差。
研究互连金属的大气等离子体处理在铜电镀工艺的有机清洗和铜抛光材料的锡/铜膜中的实际应用,在大气压下用适量氧气产生的13.56兆赫射频等离子体可以适度清洁铜箔样品上的有机颗粒,并为减少常规清洁过程中危险化学品的使用提供了封闭的可行性。此外,还研究了铜表面镀锡的大气等离子体处理,锡涂层的氧化还原可能是有益的;然而,不良的可焊性被认为是锡表面等离子体处理的一个问题,尽管通过大气等离子体处理没有显著改善金属化材料的性能,但是通过实验获得了与传统工艺相当的性能,应该继续对这一主题进行更深入的研究,以便从性能角度改善环境效益。