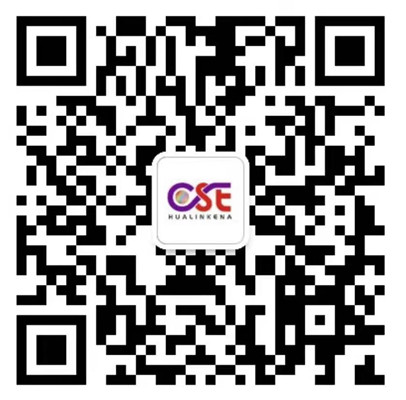
扫码添加微信,获取更多半导体相关资料
在本研究中,开发了一种包含超声波和超气体过程的系统,通过调节氢氧化铵的功率产生,晶片与超电子换能器间隙中的巨波保证了整个晶片上均匀的声能,超气能促进了自由基的产生,从而在稀溶液中去除残基,与超声波相比,氢氧化铵溶液中超气清洗的特征损伤减少。此外,大气离子清洗产生的气泡空化的机械力也提高了残渣的去除,提高了传质速率。极端的空化有利于去除颗粒,但会破坏晶圆的特性。超声波清洗造成的损伤明显大于超气清洗。
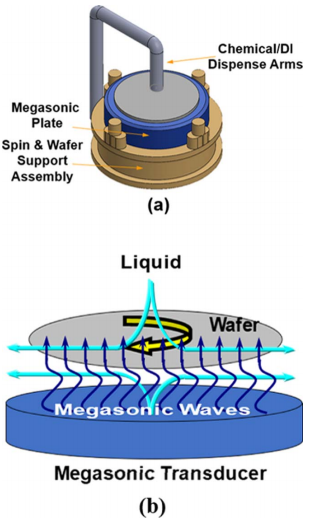
图1
图1(a)显示了本研究的超气清洗过程示意图,并显示了晶片的位置,在晶片的两侧进行巨超声清洗,在背面进行全功率清洗,在单个晶片清洗板的正面进行功率衰减,该自旋清洗工具配有径向传感器阵列,用于单晶片的大型湿式清洗,超气传感器(面积323mm)设计为0.98MHz的自旋基底(通常为0-50rpm),旋转卡盘被设计用来容纳200毫米的晶圆,用动态光散射法确定的氧化硅颗粒的尺寸为250±50nm,所有实验均在台湾半导体研究所(TSRI)的一个100级微/纳米制造中心进行,图案样品在200mm晶片上的晶片自旋清洗组件中暴露在超气体搅拌中。
实验研究了标称频率为80kHz时的超声波清洗问题,提高工艺的可重复性,并确保每个晶片的新鲜化学成分,采用双面清洗,具有不同的正面和背面化学能力,针对低颗粒进行了优化,建立了一种由氢氧化铵调节功率产生的超声和超气过程不同措施的系统。
在声功率密度为70w的情况下,用pH为8.2的氢氧化铵溶液在30s后进行(a)超气清洗,在30s后进行(b)超声清洗,如果晶片上覆盖指示性位置的大量区域被破坏,那就足够了,通过小颗粒确定了污染位点,对于超气清洗,进行PRE以确定清洗能力。首先,计数大量超过1μm的粒子,并放置在一个8英寸的晶片上,然后将晶片放入传感器设备中,通过元气搅拌建立起来,然后使用70W的功率清洗晶片以避免污染,溶液以∼5.5至6μmmin−1的流量遍布晶片,然后将样品放入颗粒计数器中计数清洗后剩余颗粒的数量。
图3
图3显示了在pH值为8.2时,氢氧化铵中发生的声功率密度与损伤密度的对比图,在溶液功率增加后,可以观察到强烈的损伤,这清楚地表明超气体系统的损伤明显低于超声波系统,图3显示了用氢氧化铵清洗后的图案碎片上的损伤部位,在pH值为8.2时,随着20W功率从20W增加到70W,氢氧化铵的缺陷密度增大,与30s的超声和超气体清洗暴露时间相比,氢氧化铵溶液中超气体清洗的特征损伤减少。
在超气清洗之前,可以在二氧化硅的侧壁上清楚地观察到聚合物残基。对200毫米晶片进行了全晶片试验,从而去除了整个残留物和颗粒。扩展纳米技术的工艺流程,以获得超气体搅拌的结果,超声有助于在评估超声搅拌能力的工艺流程中,去除器件晶片中的残留物,对于互连,物理搅拌处理似乎是优先的,只要可以限制去除残留物所需的蚀刻量,从而使介质不损坏。
从等离子体蚀刻条件切换到表面的超气体条件,有效地减少了碎片的数量和划痕的数量;缺陷的数量也略有减少,因此,巨超声清洗似乎可以减少更换标准调节器时的划痕和缺陷,在侧壁和底部,超声波后清洗产生沉重的碎片,可以附着在晶片表面,相对于超气体清洗,超声波清洗后会有更多的残留物粘在表面上。
在氢氧化铵溶液中,残留位点的大小在∼200nm的范围内,蚀刻后的残留物没有通过超声波清洗清除,而是通过超气清洗清除,巨气清洗60s后,从金属线侧壁上去除,超气搅拌的影响也应用于PR去除粒子的溶液中,大气搅拌的使用也有利于防止沉积。此外,超气搅拌不仅适合于减少缺陷,而且可以增加PR而不需要过强力,从而导致结构损伤。
本文表明,在氢氧化铵中提供高PRE的同时减少特征损伤,解答大气清洗产生的气泡空化的机械力也提高了传质率,提高了残渣的去除能力,与典型的氧化硅残留去除方法相比,该方法具有较高的残留去除效率,且材料损耗低,长宽比高。超气清洗造成的损伤明显低于超声波清洗系统,最后,首次成功地证明了纯Ge堆叠纳米片fet,在60°C下的新型选择性硅蚀刻,这些结果表明,超气清洗可应用于纳米颗粒清洗过程,巨波清洗正迅速成为集成电路制造过程中后工艺清洗的一种有效方法。