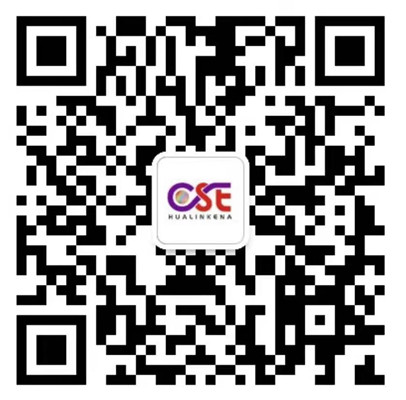
扫码添加微信,获取更多半导体相关资料
为了开发利用三氟化氯气体对碳化硅外延反应器的原位清洗工艺,研究了去除磁化体上形成的碳化硅膜的蚀刻条件和工艺。通过将蚀刻温度调节到330◦C以下,可以去除所形成的碳化硅薄膜,而不会对基座造成明显的损伤。利用化学气相沉积(碳化硅)外延晶片4氢碳化硅(碳化硅),开发了目前和未来工业所需的动力电子器件,必须通过热和等离子体增强CVD反应器的反应器清洗技术去除它们。本研究详细研究了利用三氟氯气体制备一种适用于所形成的碳化硅薄膜的碳化硅外延反应器原位清洗工艺的化学反应条件。
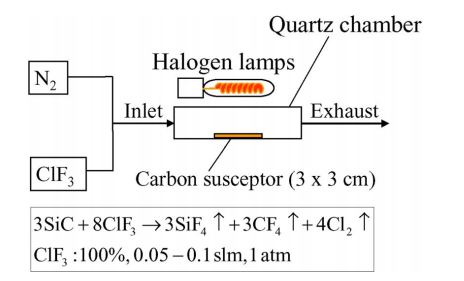
图1
图1显示了本研究中使用的反应器,以尺寸为3cm×3cm的小碳板作为基座,本研究中使用的基座由高纯碳制成,表面覆盖碳化硅涂层,与工业CVD反应堆相同,遵循4h碳化硅外延生长过程,在4h碳化硅衬底表面形成30-50μm厚的4h碳化硅外延薄膜。
为了进行蚀刻,将具有碳化硅薄膜的基座插入到水平反应器12中,如图所示1,该反应器由一个气体供应系统、一个石英室和六个红外灯组成。供气系统引入了三氟化氯气和氮气,该反应器的横截面较小,以实现三氟化氯气体的高消耗效率。石英室的高度和宽度分别为10mm和40mm,磁座通过卤素灯通过石英室壁发射的红外线加热,六盏红外灯的功率根据之前在环境氮中测量的温度进行调整。

图2
图2显示了本研究中使用的典型过程。首先,将基座在环境氮气中加热到蚀刻所需的温度。然后在不含氮气的情况下,以100%和50-100sccm暴露于三氟氯气,在将环境气体从三氟化氯交换为氮气以终止蚀刻后,将基座冷却至室温,在调整磁座温度的同时,重复进行了一组包括加热、暴露和冷却在内的步骤。由于碳化硅薄膜的形状和接触条件可能会影响化学反应的结果,使用扫描电镜对碳化硅薄膜和磁座表面之间的评估。此外,还评价了电座上碳化硅涂层膜的表面形貌和厚度。
另外评价了形成的碳化硅薄膜的厚度和接触条件,然后,评价碳化硅膜和形成的碳化体表面产生的碳化硅涂层膜的平均蚀刻速率,三氟氯气体在浓度100%、流量50sccm、大气压、温度320◦C下进行蚀刻,通过蚀刻前后的重量下降来评价蚀刻速率,考虑到形成膜的不均匀性,本研究得到的蚀刻率为磁座表面的平均值。所形成的碳化硅膜的平均刻蚀速率为0.79μmmin−1,而碳化硅涂层膜的平均刻蚀速率为0.18μmmin−1。所形成的膜的蚀刻率大约是基座涂层膜的四倍。这表明,当根据薄膜厚度及其表面状况仔细调整蚀刻期时,可以进行现场清洗。
由于覆盖整个基座表面的顶层可以通过290◦C快速刻蚀掉,所以这一层可能由富含硅的碳化硅组成,由于三氟化氯气体的硅蚀刻速率相当高,预计蚀刻速率会随着硅含量的增加而增加,接下来,区域C被认为是3C-碳化硅,因为黄色是3C-碳化硅的特征。
虽然本研究假设了每一层的多聚型,但还需要通过x射线衍射法、x射线光电子显微镜和能量色散x射线光谱法等一些方法来确定,堆叠层结构可随反应堆和工艺而发生变化,因此,聚型和成分的信息将有助于精细优化清洗条件。在将清洗过程应用于外延反应器时,应注意三氟氯气体造成的氟污染。在外延生长过程中,将三氟氯气体清洗的碳基体放置在4h-碳化硅衬底附近时,幸运的是,外延薄膜没有明显的污染。然而,还需要进行进一步的评估。