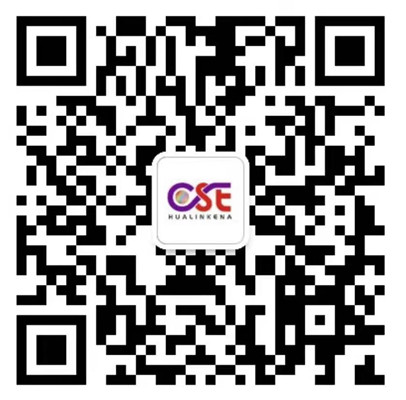
扫码添加微信,获取更多半导体相关资料
引言
作为半导体器件和MEMS微加工技术基础的光刻技术中,显影和清洗等湿法工艺是必不可少的。在本稿中,介绍了能够定量评价超临界CO2处理对微细光刻胶图案―基板间的粘接强度带来的影响的、用于微小结构材料的粘接强度试验法。 并且,实际利用该试验法,测量在不同的超临界CO2处理条件下制作的微细光刻胶图案的粘附强度,通过超临界处理条件提高粘附强度的定量性证明了这一点。
实验
该微细加工技术还应用于Micro―electro―mechanical system(MEMS)器件的微机械元件的制造。 MEMS器件是指在基板上集成由数~数百微米尺寸的部件构成的微机械元件和电子电路。 图1显示的是一般的半导体·MEMS微加工技术的示意图。 图1左图是作为半导体器件制造基础的二维微细加工技术,利用光刻法,在通过旋涂等在基板上薄薄涂布的感光性光刻胶膜上,利用紫外线、电子束等对微细图案进行曝光、显影,从而在基板上用高分子光刻胶薄膜制作超微细图案的技术。 通过利用该微细抗蚀剂图案作为掩模对基板上的薄膜进行蚀刻,或者利用该微细抗蚀剂图案作为模具进行气相沉积、电镀等,在基板上制作高密度集成电路。
在MEMS器件中,通过组合该二维光刻法和三维微加工双方的微细加工技术并反复实施,同时进行超微细电子电路和微小机械要素的制造、组装。
如前项所述,由于急剧的高集成化,光刻胶的图案宽度急剧减少,与此相对,光刻胶膜厚的减少率较低,其结果是微细光刻胶图案的高长宽比(图案高度/图案宽度)化得到了发展。
为了解决显微抗蚀剂图案与各种溶液之间起作用的表面张力的问题。 图2显示的是由于超细微抗蚀剂图案的细微化、狭窄化、高长宽比化而产生的新问题的模式图。 在显影·清洗等湿法工艺中,由于光刻胶图案变窄·高长宽比化,在表面张力的影响下,各种溶液向光刻胶图案间的侵入·循环·排出受到阻碍(图2上图)。 因此,没有足够的新鲜溶液供应到微细化的光刻胶图案内部的各个角落,导致微细化图案的显影不良和图案底部的清洗不良。 而且,在利用微细图案的电镀和蚀刻等湿法工艺中,如果向图案内部的新鲜溶液循环受到阻碍,反应就无法进行,因此会发生电镀不良和蚀刻不良等各种问题。 另一方面,在干燥过程中,由于毛细力的影响,在超微细化和高纵横比的抗蚀剂图案的间隙中残留大量溶液,并且由于图案内部的毛细力和外部的气压之间的差,在图案外部产生力。
以下介绍实际将超临界CO2应用于光刻的显影·清洗·干燥工序等的研究事例。 作为将超临界CO2应用于光刻显影的例子,有利用超临界CO2溶解某种高分子的性质,用超临界CO2成功显影导入了甲基硅氧烷结构和碳氟化合物结构的光刻胶的研究14),15)。 此外,还进行了在加入添加剂的超临界CO2溶剂中可显影的EUV曝光用光刻胶的开发16),17),以及为使极性聚合物的显影成为可能的向超临界CO2溶剂中添加氟化铵盐等的研究开发。
为了防止这种情况的发生,需要对微细光刻胶图案的粘接强度和工艺条件的关系进行定量评价的方法。构成半导体·MEMS器件的微小结构部件大多是为了制作微小尺寸的部件而新开发的材料,或者用特殊的制造法制作的。 由于这些只能通过微小尺寸得到,因此不能适用于使用通常尺寸的试验片的材料评价试验,其机械特性有很多不明确之处。 而且,微结构材料的机械特性受到光刻和微加工等各工艺条件的强烈影响,但由于工艺工序涉及多个方面,其影响程度目前还不清楚。
由于试验简便,因此在研究开发现场被广泛实施。 但是,该方法可以判定胶带-试料间的附着力和基板-试料间的附着力中哪一个更强,因此很难进行严密的定量评价。 除此之外,作为能够对基板上制作的薄膜进行直接试验的方法,还有划痕试验另一方面,关于以MEMS的微机械要素等基板上制作的三维微小结构材料为对象的定量粘接强度评价法,目前还没有国内外的试验标准。 因此,对于三维精细结构材料的定量粘附强度评估,需要统一的测试标准。
因此,下面整理了以三维微小结构物为对象的定量粘接强度评价法标准化的必要条件。 首先是试验片形状,考虑到要进行各种工艺条件的评价,粘接强度试验片最好是制作容易、工艺工序少的简单形状。 其次是试验方法,为了能够适用于大范围的试验机,要求试件的保持方法和对齐方法,以及对试件的加载方法要简单且容易。 另外,一般情况下,粘接强度数据有很大的偏差,因此有必要对试验结果进行统计分析。
该微小结构部件的粘接强度测量中使用的试验装置的必要条件为:①具有能够将加载夹具移动到微小圆柱形试验片的加载位置的精密定位机构;②具有能够以一定位移速度对微小尺寸试验片进行精确位移的机构;③具有能够精确测量、记录当时负荷的系统。
在此,展示了实际使用抗蚀剂材料制作微小圆柱图案,进行微小圆柱试验片―基板间的粘接强度试验,评价超临界CO2工艺的例子。 本例使用的是以永久使用为目的开发的环氧系厚膜抗蚀剂SU-8。 SU-8是利用通用的紫外线曝光的光刻法,可以容易地制作厚膜、高长宽比的微细结构物,因此作为发挥低弹性模量和穿透性等特征的永久使用的微细结构部件,有望应用于悬臂梁、微流路、光波导等领域的光刻胶。 使用该SU―8,在15 mm见方的硅基板上,通过光刻法在同一工艺条件下,制作了多个圆柱直径125μm、圆柱长度78―110μm的微小圆柱试验片。
表1表示超临界CO2处理条件的例子。 在本例中,将SU―8微小圆柱试验片的基板分成两部分,在相同条件下进行超临界CO2处理后,分别在不同条件下进行减压工序。
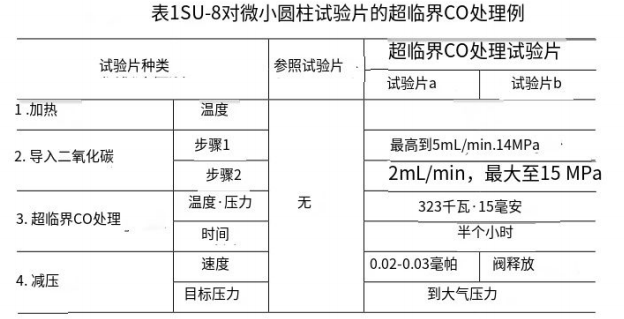
表1
上述结果表明,在光刻的超临界CO2处理中,如果控制减压条件,就有可能提高SU―8微小光刻图案的粘合强度。 像这个例子一样,通过系统地改变超临界CO2处理条件,定量地评价对微小光刻胶材料的粘着强度带来的影响,可以认为这将有助于将超临界CO2工艺更积极地应用于光刻工艺。
讨论和总结
本文在整理利用超临界二氧化碳的半导体·MEMS的微细加工技术中可能发生的问题点的基础上,介绍了能够定量评价工艺对微细光刻胶图案-基板间的粘附强度的影响的用于微小结构材料的粘附强度试验法。 超临界二氧化碳处理作为解决在年复一年的微细化、高长宽比化、复杂化的微小加工技术中产生的表面张力和毛细管力问题的方法是非常值得期待的,但另一方面,对高分子抗蚀剂材料的影响,特别是对粘着强度的影响也令人担忧。
为了积极推进超临界二氧化碳处理技术的实用化,有必要定量评价该工艺对微小图案的强度和附着力等机械性能的影响,保证其安全性。 而且,如果能够明确工艺条件和微小图案材料的机械性能的关系,就有可能通过超临界二氧化碳处理积极地进行高分子的改质等。 微小尺寸材料的机械性能评价将成为将超临界二氧化碳处理积极应用于半导体制造技术的关键。