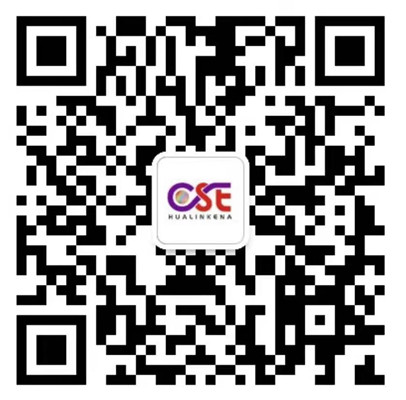
扫码添加微信,获取更多半导体相关资料
微透镜及其阵列在光子学中有许多应用的可能性,规模不断缩小。它们因能够在微型尺度上操纵光线并使整体包装简单紧凑而变得流行。因此,预计光子学中的微透镜应用将以各种形式广泛传播。
我们使用基于Br2溶液的扩散限制化学蚀刻技术制造了折射半导体微透镜。简单的一步湿法刻蚀工艺产生了高质量的GaAs和磷化铟微透镜,这两种半导体材料在光电子学中最受欢迎。标称透镜直径为30 m的球形GaAs微透镜分别具有91和36 m的曲率半径和焦距。经原子力显微镜检查,表面粗糙度测量值低于10。由于加工简单和高质量的结果,这种微透镜制造方法应该易于应用。
图1示意性地示出了掩模孔内的蚀刻工艺。Br2分子在掩蔽区域不与衬底反应,这些分子必须扩散到开放区域(在我们的例子中是圆孔)进行蚀刻。然而,由于Br2分子的低迁移率,分子在掩模边界附近被消耗的概率高于远离掩模边界的概率。蚀刻窗口上蚀刻速率的这种逐渐的空间变化(其分布在图1的上面板中示意性地示出)在半导体表面上形成球面透镜轮廓。在取决于半导体材料和所需透镜曲线的蚀刻期间,样品需要静止放置在蚀刻槽内以获得良好的再现性,因为对蚀刻物质的自然差异运动的任何干扰都会改变蚀刻过程的细节。
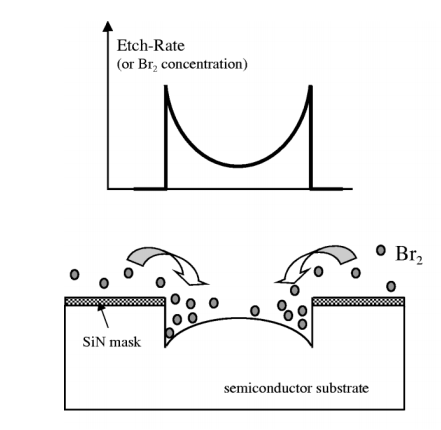
图1 使用基于Br2的扩散限制蚀刻的半导体微透镜制造工艺的示意图
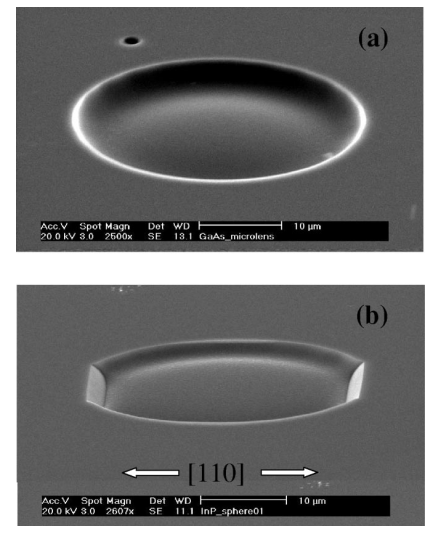
图2 通过所提出的工艺制造的:(a) GaAs和(b)磷化铟微透镜的扫描电镜图像。刻面形成在InP微透镜中,但仅在蚀刻的侧壁上
图2显示了的扫描电子显微镜(SEM)图像通过上述方法在GaAs衬底和磷化铟衬底的(001)表面上形成的微透镜。对于GaAs和磷化铟微透镜,氮化硅蚀刻孔的深度保持不变(30 μm),而蚀刻持续时间分别为15和5分钟。如图2(b)所示,InP微透镜沿[110]方向出现小刻面,我们将其归因于所用蚀刻剂和InP的特定组合中的部分反应速率受限蚀刻成分。这种刻面可能导致镜片轮廓的轻微不对称。尽管如此,在镜片本身的表面上没有观察到明显的刻面。
为了对透镜轮廓进行详细的定量评估,我们采用了原子力显微镜技术。图3示出了根据测量的AFM数据构建的GaAs微透镜的全尺寸透视图像。图4(a)中表示的是沿着穿过透镜中心的线的透镜轮廓,也是从二维原子力显微镜数据重建的。虚线是基于球面透镜近似的理论拟合。根据拟合估计的透镜曲率半径和焦距分别为91和36 m。
然而,焦距(因此镜头速度)可以很容易地控制,通过下面描述的两种方法中的任何一种。首先是空间控制,其中掩模孔直径被扩大到超过蚀刻物质的扩散长度,使得透镜中心附近的蚀刻速率斜率变小。孔的尺寸越大,透镜轮廓越平坦。我们的方法对孔径大小没有实际限制。我们已经尝试了高达120米的镜头直径,并观察到与30米的情况相当的相位误差。更有用的是时间控制,其中蚀刻时间用作方便的透镜曲率控制参数。随着蚀刻时间变长,透镜边缘和中心之间的蚀刻深度差变得更加显著,导致更清晰的透镜轮廓。
表面粗糙度也是微透镜的一个重要问题。图4(b)是图4(a)中所示的透镜轮廓的中心区域的放大图——对于适当的缩放,数据在减去拟合的背景轮廓之后呈现。除了零基线周围的逐渐调制(反映球面像差或测量数据和拟合之间的差异),透镜表面的局部粗糙度保持在10以下。Br2蚀刻表面的这种极端平滑性已经被集成了垂直模式转换器的高性能InP激光二极管所证明。
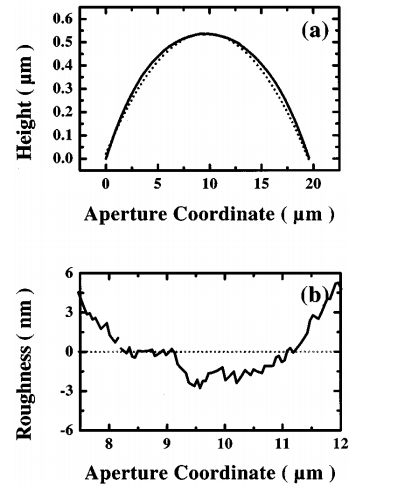
图4 (a)GaAs微透镜沿着穿过透镜中心的线的表面轮廓(实线),以及球面拟合(虚线)。(b)靠近透镜中心的放大轮廓,以显示表面粗糙度
我们还检查了整个晶圆上加工微透镜的空间均匀性,以及我们加工的连续再现性。对于周期为250米的30米GaAs微透镜的10×10阵列,焦距的标准偏差估计为1.8米,平均焦距为36米的5%。由于边缘效应的减少,随着透镜阵列的增大,这种偏差预计会进一步改善。另一方面,在同一批蚀刻剂中,间隔3小时的两次连续运行之间的平均焦距差小于1米,证明了我们的方法的良好运行再现性。
总之,我们将一步扩散限制化学蚀刻技术应用于GaAs和磷化铟,以制造表面粗糙度低于10的高质量微透镜。从各种优点来看,包括制造工艺的简单性和透镜曲率随蚀刻时间的方便的原位控制,我们相信本文提出和展示的微透镜制造方法对于光子器件集成和未来的光子超大规模集成电路器件制造是理想的。