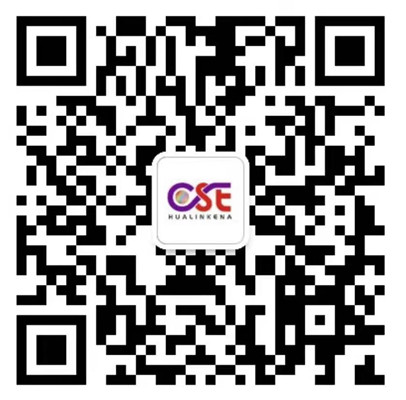
扫码添加微信,获取更多半导体相关资料
引言
在镶嵌集成方案中,铜被用作互连材料。在镶嵌集成方案中,通过等离子体工艺的蚀刻处理导致形成聚合物残留物、在电介质侧壁上溅射的铜、通孔底部的铜氧化以及硬掩模表面的铜沉淀。为了去除这些杂质,必须进行通孔后蚀刻清洗。
我们测试了几种由稀释的氟化氢和有机酸组成的含水清洗溶液。稀释的氟化氢主要用于去除聚合物残留物和有机酸,以清洁铜表面。这些混合物已经被研究过,并且与几种多孔和致密的ULK材料相容。本文研究了稀氢氟酸溶液中有机酸和气泡对铜和氧化铜溶解速率的影响。首先,通过X射线反射仪表征确定的铜溶解动力学获得氧化铜和铜蚀刻速率和粗糙度。其次,进行形态计算以解释作为溶液和气体鼓泡的函数的铜蚀刻速率差异。
实验
通过在硅衬底上100-150的TiN层上沉积500的铜(PVD)层来制备200 mm样品。将铜晶片暴露在洁净室气氛中,以获得几埃(35至40埃)的氧化铜膜。测试了几种含有3.5重量%有机酸或稀释的0.05重量%氟化氢加3.5重量%有机酸的溶液(水基化学)(表1)。通过O2或N2气体鼓泡来调节溶液中的气体含量。
表1 测试的清洗溶液
对于动力学研究,将相同的铜样品在25℃的溶液中浸浴30秒至4分钟,在5分钟内漂洗并干燥,并在每次浸浴后用x光反射计(XRR)表征。实验X射线反射率曲线是用程序Firefx4c_6 用Parrat方法模拟的。该程序用于根据电子密度厚度和几个层的粗糙度将实验反射率曲线调整到模型。由XRR确定的铜粗糙度对应于由辐射波长限制的短长度尺度的粗糙度,该粗糙度不同于由原子力显微镜确定的粗糙度,对尖端宽度以下的横向变化敏感。根据铜溶解的动力学,确定作为清洗持续时间的函数的氧化铜和铜蚀刻速率以及粗糙度的变化。
结果和讨论
铜和氧化铜蚀刻速率:所有测试溶液中的氧化铜蚀刻速率均高于150A.min-1。铜在有机酸和dHF +有机酸溶液中的溶解速率用相同的方法计算,如图1所示。
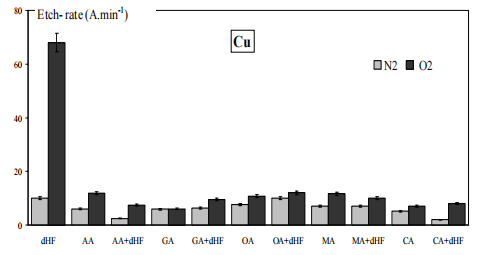
图1 在N2和氧气鼓泡的水溶液中铜的蚀刻速率
首先,在有机酸和dHF +有机酸溶液中铜的腐蚀速率接近并低于13.min-1。其次,气体鼓泡的影响在dHF中非常重要。事实上,在O2鼓泡下,铜在dHF中的腐蚀是在N2鼓泡下的7倍。相反,在含有有机酸的溶液中的O2鼓泡导致铜蚀刻速率的非常低的增加(接近不确定性)。
短长度尺度下的铜粗糙度:图2和图3显示了在dHF、有机酸和dHF +有机酸溶液中,样品粗糙度随清洗时间的变化。在N2鼓泡下,在所有含有机酸的溶液和dHF溶液中清洗的铜样品也观察到同样的变化。清洗30s后,无论使用何种清洗溶液,粗糙度值都大致相同。对于较高的清洗持续时间,O2鼓泡的dHF导致铜粗糙度线性增加,而铜粗糙度在其他溶液中保持不变。这种增加可能是由高铜蚀刻速率引起的。
物种形成计算:为了解释铜溶解的机理,用JChess软件进行了形态计算。目标是在浸铜之前确定溶液中存在的物质。例如,乙醇酸的情况将被处理。
如图4所示,考虑到不确定性,无论气体如何鼓泡,镓和dHF+GA溶液中的铜蚀刻速率都是相似的。这可以用两种溶液中相似的酸碱度以及相似的酸和相关的碱浓度来解释(图5)。氧气含量对酸碱度变化没有影响。在有氧气鼓泡的dHF溶液中,铜的腐蚀速率高于其他溶液。

图4 在N2和氧气鼓泡条件下,镓、镓+氢氧化铪和氢氧化铪溶液中的铜蚀刻速率。显示溶液的酸碱度
总结
稀释的氟化氢和有机酸的混合物是一种低成本(简单)和ESH(稀释)的清洁溶液。无论溶液中的氧含量如何,在稀释的氟化氢溶液中加入有机酸都可以更好地控制铜的溶解速度。