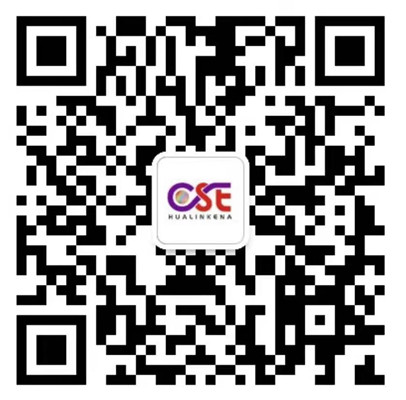
扫码添加微信,获取更多半导体相关资料
摘要
在印刷和蚀刻生产厚金属膜中的精密图案时,需要对化学蚀刻剂有基本的了解,以实现工艺优化和工艺控制。为了蚀刻纯铝电路,研究了正磷酸、多磷酸和氯化铁的配方。 研究的目的是确定蚀刻速率和图案定义对正磷酸浓度从50%到 95%(v/v)s多磷酸浓度从50%到5%的变化的敏感性(v/v),氯化铁(III)浓度为10-40g/L,溶解铝浓度为0.0-5.0g/L。 得出的结论是,正磷酸、多磷酸、氯化铁蚀刻剂系统允许蚀刻 剂制备和电路处理的合理变化,而不会显著影响蚀刻的纯铝电 路的线宽减小和边缘质量。
在所研究的范围内,在正磷酸浓度为75%至95%和氯化铁浓度 为10g/LB寸,可获得最佳的图案清晰度和线宽减小。为了保持这种最佳状态,需要温度控制和对蚀刻产物积累的密切监控,建立了原子吸收分光光度法测定溶解铝浓度的方法。
未来的工作将包括评估溴化铁、硫酸化铁和过渡金属氧化物盐,如镍、钴、锰、钌和锇,作为氧化铁的可能代替品。其他研究将集中在蚀刻反应的分析特征上。
介绍
在印刷电路工业中,化学蚀刻长期以来一直是在金属膜中产生精确图案的公认方法。蚀刻结合目前的光刻技术,提供了亚微米线分辨率。尽管随着图案尺寸数量级接近晶粒尺寸,电路图案的生产趋向于添加“剥离”技术,但是化学蚀刻仍然是图案生产的重要方法。
本研究的目的是表征铝蚀刻速率和图案定义对浓度、温度、氯化铁浓度以及正磷酸浓度、多磷酸条件下溶解铝浓度变化的敏感性,并将所得蚀'刻质量与这些工艺变量关联起来。
实验法
将样品放置在垂直于蚀刻剂流的样品平面上(图1)。蚀刻速率由蚀刻时间和样品铝厚度决定。通过目测确定蚀刻终点。铝的厚度是根据在冲压样品的材料上进行的β反向散射测量确定的。样品由127um厚的kapton制备,在该kapton上通过物理气相沉积(PVD)已经沉积了 127 um的99.999%的铝。
Kapton样品上的每个PVD铝被冲压成1.346厘米的直径。在所有情况 下,除非另有说明,样品由涂有PVD铝的Kapton制备,在该铝上已经显影了光致抗蚀剂图案。该图案由一条860 um宽的线组成,该线位于1.42 cm2样品区域。光致抗蚀剂图案线宽的定义和减少用于描述蚀刻质量。为了量化线宽减小 ,用闭路电视系统(CCTV)以75X测量蚀刻前的光致抗蚀剂图案宽度和蚀刻后的电路线图案宽度。蚀刻前后对样品进行光显微照相(50X)。
结果和讨论
温度的影响:尽管蚀刻反应的机理至今未被报道,但希望知道蚀刻过程中蚀刻速率如何变化。 在一个测试中,在蚀刻期间监测样品铝的重量损失。发现铝的蚀刻速率在蚀刻期间是恒定的,并且样品重量损失和经过时间之间呈现线性关系(图2)。由于这一特性,选择铝薄膜的视觉消失作为蚀刻终点被认为是合理的,尽管缺乏假定的蚀刻反应机理。
氯化铁的作用:虽然氯化铁的存在对于蚀刻浴来说不是必需的,但是蚀刻速率和蚀刻质量对氯化铁浓度很敏感,如图7和图8所示,在60°C和70 °C时,存
在10至20 g/L的范围,其中氯化铁浓度的增加与蚀刻速率的增加相关。数据表明(图7至图9),蚀刻速率不敏感,铁(iii)氧化物浓度低于10克/升这一迹象可能需要进一步证实。

图 7
正磷酸浓度的影响:在所研究的范围内,蚀刻速率和正磷酸浓度之间的关系是直接比例关系( 图10至12)。尽管在恒定温度下,正磷酸浓度和铝蚀刻速率之间的指示关系是清楚的,但正磷酸和线宽减小之间的关系并不那么确定(图4至图6)。在较高的温度下(图6),数据似乎表明增加正磷酸浓度的一般效果是减少线宽的减少。
蚀刻剂中铝和总铁浓度的测定方法:测定铝和总铁的分析方法,以监测镀液成分的变化。这分析方法直接使用蚀刻剂,无需预先进行化学分离进行分析。通过校准由不同浓度的溶解铝组成的一系列合成蚀刻剂溶液的吸光度,确定了铝测定方法的准确性。每种合成溶液代表不同比例的溶解铝与磷酸盐背景。将这些合成溶液与标准铝进行比较发现硫酸溶液的铝离子浓度在2-50 ppm范围内,吸光度完全一致。对于总铁的类似校准,合成溶液和铁(iii)之间有3%的一致性氯化物标准。无铝蚀刻剂的吸光度与去离子水的吸光度相同。该方法的检出限为2 ppm。原子吸收分光光度法可作为一种快速、简便的定量分析方法,用于测定镀液中的溶解铝和总铁。