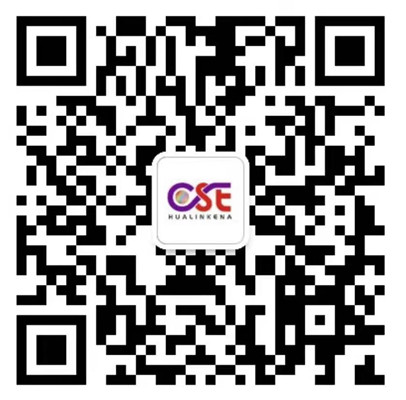
扫码添加微信,获取更多半导体相关资料
引言
氢氧化钾溶液通常用于改善硅(100)表面光滑度和减少三维硅结构的凸角底切。异丙醇降低了氢氧化钾溶液的表面张力,改变了硅的蚀刻各向异性,显著降低了(110)和(hh1)面的蚀刻速率,并在较小程度上降低了(100)和(h11)面的蚀刻速率。
为了在低氢氧化钾浓度下获得低粗糙度的(100)表面,蚀刻溶液必须含有饱和水平的异丙醇。在我们的研究中,我们研究了异丙醇浓度对具有不同晶体取向的硅衬底的蚀刻速率和表面形态的影响。还研究了氢氧化钾浓度对(hkl)面蚀刻速率的影响。为了更好地理解蚀刻过程中在硅表面上发生的现象,还进行了蚀刻溶液的表面张力测量。最后,给出了在硅(100)晶片上制作的(hkl)侧壁面包围结构的例子。
实验细节
实验中使用了不同(hkl)取向的单晶硅片。没有研究具有(111)取向的晶片,因为该平面在所有碱性溶液中的蚀刻速率非常低。因此,我们假设(111)蚀刻速率等于零。晶片在含有不同浓度异丙醇的3-10 M氢氧化钾水溶液中蚀刻。含有过量醇的溶液使得单独的醇层漂浮在溶液表面上,然后被认为是饱和的(与醇浓度低于饱和水平的溶液相反,其然后被认为是非饱和的)。蚀刻过程在75℃的恒温玻璃容器中进行60分钟。采用210转/分的机械搅拌。用于制造微镜结构的(100)晶片在光刻工艺中被热氧化和图案化。
结果和讨论
异丙醇蚀刻溶液的表面张力:略
氢氧化钾浓度对蚀刻速率的影响:图2显示了(hkl)平面在不同氢氧化物浓度的纯KOH水溶液中的蚀刻速率。氢氧化钾浓度从3到5 M的增加导致所有平面的蚀刻速率的增加。然而,当氢氧化钾浓度较高(10 M)时,大多数平面的蚀刻速率降低(除了(110)平面)。在整个研究浓度范围内,(100)面比(110)面蚀刻得慢。用异丙醇饱和的3-10 M氢氧化钾溶液中(hkl)平面的蚀刻速率如图3所示,在低浓度的氢氧化钾(3-5 M)下,氢氧化钾浓度的增加会导致(100)蚀刻速率的略微增加和其邻近平面((h11)平面)蚀刻速率的显著增加,而几乎不影响(110)和(331)平面的蚀刻速率。氢氧化钾浓度的进一步增加(从5到10微米)导致(100)和(311)平面以及(110)和(331)平面的蚀刻速率增加。然而,( 110)蚀刻速率增加了大约两倍,而(100)蚀刻速率仅略有变化,这导致更高的(110)/(100)蚀刻速率比。较低的(110)/(100)蚀刻速率比通常有利于体微加工。
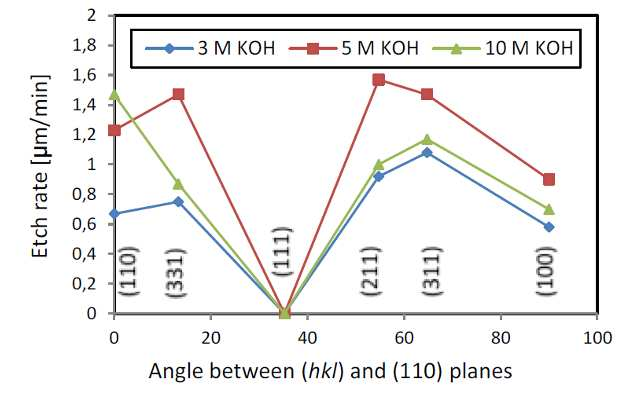
图2 在3-10M氢氧化钾溶液中蚀刻Si(hkl)底物的蚀速率
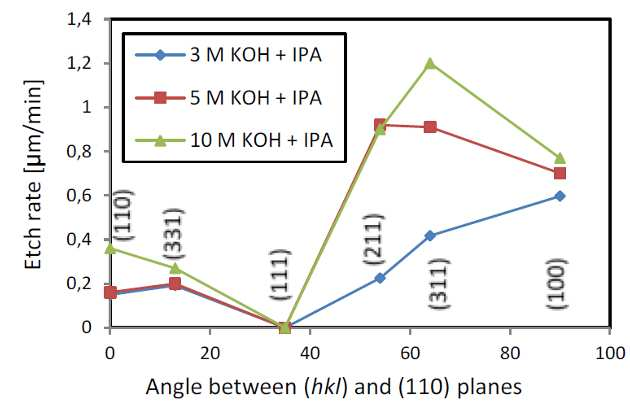
图3 在饱和IPA的3-10M氢氧化钾溶液中蚀刻的Si(hkl)底物的刻蚀速率
异丙醇浓度对(hkl)平面表面形态和蚀刻速率的影响:异丙醇浓度对表面形貌的影响取决于硅基底的晶体取向。一般来说,在非饱和溶液中,(110)和邻近平面比(100)和邻近平面更平滑,它们上覆盖着山丘(以平面为界的凸结构)。小山丘的密度随着酒精浓度的增加而减小,这在(100)表面是最明显的。当异丙醇浓度增加时,(221)的表面形态也没有改善。(331)表面是所有考虑的(hkl)取向基质中最平滑的一个。当溶液达到饱和水平时,其形态略有改善。
结论
本文研究了氢氧化钾和异丙醇浓度对硅(hkl)表面腐蚀特性的影响。当纯氢氧化钾溶液的氢氧化物浓度稍微增加(从3到5 M)时,所有被检查(hkl)平面的蚀刻速率增加。在不饱和异丙醇的氢氧化钾溶液中,在恒定的表面张力值下,也观察到蚀刻速率增加。在用醇饱和的溶液中,氢氧化钾浓度的相同增加导致(110)和(hh1)蚀刻速率的改变可以忽略不计。当氢氧化物浓度从5到10 μm变化时,纯氢氧化钾溶液中大部分平面的蚀刻速率降低,而用异丙醇饱和的氢氧化钾溶液中大部分平面的蚀刻速率增加。这一事实可以用酒精浓度随着氢氧化钾浓度从5到10毫摩尔的增加而降低来解释。
测量蚀刻溶液的表面张力。在较宽的氢氧化物浓度范围内,随着醇浓度的增加,表面张力降低。这些结果表明,在空气/蚀刻溶液界面处以及类似地在蚀刻溶液/硅界面处,醇分子的密度应该增加到饱和水平。然而,蚀刻结果与这一理论有部分矛盾。当酒精浓度达到饱和水平时,观察到(100)和(311)蚀刻速率明显增加。这表明在饱和水平下,硅表面的单层醇分子部分消失。