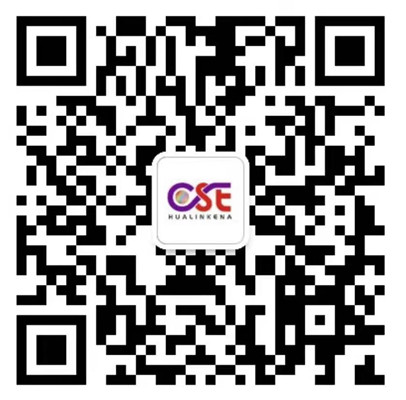
扫码添加微信,获取更多半导体相关资料
摘要
封装小型化这一永无止境的趋势将半导体工业推向了技术的边缘。因此,有必要开发新技术,以满足对先进和先进工艺能力的需求。
这篇论文是关于在圣卡兰巴开发和安装强大的50µm晶圆减薄和切割能力的挑战。随着硅片被磨得越薄,它对机械应力和振动越敏感。传统的机械切割工艺在切割过程中会产生大量的机械应力和振动,这往往会导致背面切屑和模具裂纹问题。背面碎屑作为骰子背面的断裂点,显著降低其模具强度。这一难题通过使用一种突破性的技术——磨削前切割(DBG)得到解决。
介绍
传统工艺包括晶圆贴带、晶圆背磨、脱模和晶圆安装,然后是晶圆锯。
晶圆制备工艺从背面研磨开始,或者在晶圆包带过程中将BG带层压到晶圆的活动面上。BG胶带起到保护作用,以防止在下一个工艺步骤中损坏或划伤晶圆的活动面。在晶圆背面研磨时,BG胶带起到缓冲作用,并确保晶圆在整个加工过程中都被正确抽真空。一旦达到目标晶圆厚度,晶圆随后进入晶圆安装过程。研磨后的晶圆安装在切割带或切割模附膜(DDAF)和环形框架上。最后,机械晶片锯切或切割。
机械晶圆锯工艺使用刀片作为研磨机,可以分离骰子。刀片主要由磨粒和粘合剂组成。粘合剂所含的磨料用于切割模具。
结果和分析
气泡、晶须,评估结果可归纳为焊盘污染。气泡见表4。在BG胶带和半切工艺之间存在空气后,使用可能影响最终晶圆厚度和显微镜的高功率测量晶圆监测顶面碎屑。另一方面,气泡会造成模具裂纹。晶须是指晶须、键合垫污染以及使用高倍半切割区域观察到的BG带残留在条件边缘的安装情况,这可能是晶片安装过程后的外来显微镜。最后,焊盘污染是讨论的重点。
在晶圆反磨过程中,达到了目标厚度。如图14所示,从晶片背面和整个DAF上未观察到裂纹迹象良好的晶片层压条件,没有气泡和模具侧壁迹象。DBG工艺后模具飞出。图17显示了与传统晶圆锯切工艺相比,所有DAF(7µm至30µm)层压条件。结果在前几页上,DBG显著增加,因此,DAF厚度没有明显改善。DAF层压条件不同。
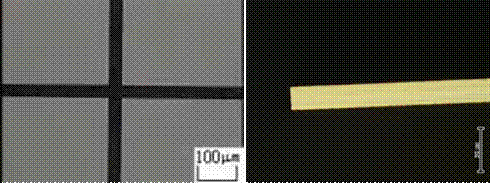
图14 显示DBG工艺结果的模具背面和侧面照片

图17 晶圆安装条件
结论
基于实验设计,进行了切割前研磨工艺的开发。半切划片应保持主轴转速为40至50k rpm,以实现良好的顶面划片响应。部分切割深度、晶圆厚度和背面削片显示稳定的工艺,规格为+/-2.5µm。在BG胶带层压过程中,为了消除晶须、气泡和污染,工艺应使用BG胶带E-1,与E-2相比,其在紫外线前的附着力更低。此外,BG胶带E-1必须在室温下层压,以达到最佳状态。最后,晶片层压显示从7µm到30µm DAF厚度没有显著影响。因此,DBG工艺可提供获得50µm最终厚度的无缺陷工艺。
文章全部详情,请加华林科纳V了解:壹叁叁伍捌零陆肆叁叁叁