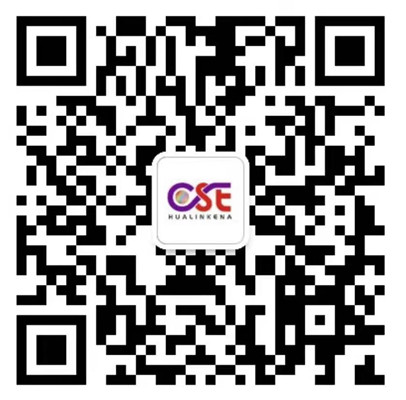
扫码添加微信,获取更多半导体相关资料
摘要
随着每一个新的先进技术节点,最小特征尺寸不断缩小。因此,设备变得更密集,曝光工具的焦深降低——使光刻成为工艺流程中最关键的模块之一。因此,消除由背面缺陷引起的热点是一个需要解决的关键问题,以防止显着的良率下降。
关键词:洗涤器,抛光清洁,背面缺陷,热点
简介
随着先进技术节点在新薄膜材料/新化学品/新集成方案方面的进步和变得更加复杂,所需的工艺/测量步骤数量急剧增加,以实现新功能(例如 FiNFET)并满足日益严格的要求。性能要求。晶圆正面缺陷的检测历来是半导体器件制造商最关心的问题,而很少关注位于背面的缺陷。背面晶圆质量正成为一个具有挑战性的问题,因为光刻 DOF 和重叠容限随着 1x 节点及更多节点处所需的器件几何尺寸缩小而降低 。在7nm等先进技术节点。
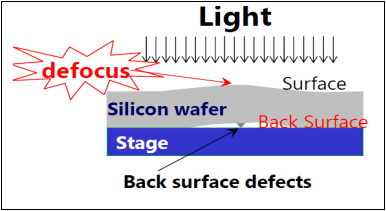
图 1:晶圆背面缺陷导致散焦问题
典型晶圆背面的光学图片如图 2 所示。晶圆背面的缺陷可能有多种来源,主要可分为颗粒、残留物和划痕。晶圆背面的颗粒和划痕(通常呈同心环形式)可由晶圆处理部件(如卡盘和机械臂)以及 CMP 工艺引起。由于不需要的薄膜去除不完全或清洁化学品的使用无效,残留物可能会留在晶片背面。此外,当晶片从一个工具移动到另一个工具,通过生产线时,会发生晶片和处理设备的交叉污染。背面缺陷会在曝光过程中扭曲晶圆的平整度并导致光刻热点,从而导致光刻问题。如果在蚀刻之前检测到热点,晶圆可以返工;否则,晶圆必须报废,否则会造成显着的良率损失。
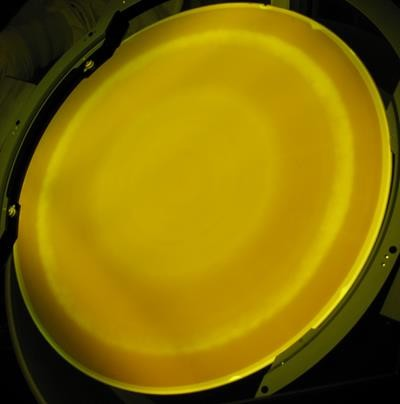
图 2:显示晶圆背面的典型光学图片
背面抛光清洁
对于抛光清洁方法,将在尖端上安装有金刚石胶带的移动抛光头应用于整个晶片背面,以去除表面凸起和颗粒。晶圆正面浸入 DIW 缓冲器中,无需物理接触坚硬的表面。可以通过改变胶带上的金刚石磨粒大小或简单地改变抛光时间来调节抛光量。在抛光过程中仅使用 DIW,并且不使用任何化学物质进行任何蚀刻和清洁操作。设备和工艺设置与之前研究中的相似。
结论
在这篇文章中,使用 7nm MOL 晶圆比较了传统湿式洗涤器清洁和晶圆背面抛光清洁的性能。使用 DIW 和室温 SC1 清洁洗涤器不会减少背面颗粒。即使使用 HF 和热 SC1,粒子计数也没有显着改善。在洗涤器清洁中添加刷子带来了边际改善。另一方面,仅通过 DIW 机械抛光进行背面清洁可使背面颗粒减少约 60%,并且可以在整个下游工艺步骤到 M1 CMP 期间保持低颗粒数。然而,抛光清洁方法会导致晶片局部形状曲率的显着增加,并且需要解决其对光刻覆盖的潜在负面影响。
文章全部详情,请加华林科纳V了解:壹叁叁伍捌零陆肆叁叁叁