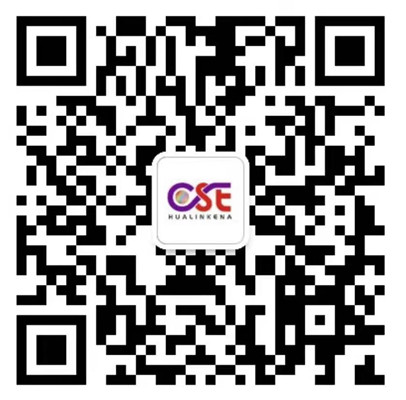
扫码添加微信,获取更多半导体相关资料
介绍
根据器件的具体类型,硅集成电路的制造需要500-600个工艺步骤。大多数步骤都是在将完整的晶片切割成单个芯片之前,以单元工艺的形式执行的。大约30%的步骤是清洁操作,这表明清洁和表面处理的重要性。
硅电路的器件性能、可靠性和产品产量受到晶片或器件表面上化学污染物和颗粒杂质的严重影响。因此,由于半导体表面的极端敏感性和器件特征的纳米尺寸,在热处理如氧化之前、通过蚀刻形成图案之后、离子注入之后以及薄膜沉积之前和之后清洁硅晶片的有效技术是至关重要的。因此,在硅片中制备超洁净材料已经成为先进集成电路制造的关键技术之一。
人们可能会问必须消除的杂质的性质、类型和来源。晶片表面的污染物以吸附的离子和元素、薄膜、离散粒子、微粒(粒子簇)和吸附气体的形式存在。表面污染物薄膜和颗粒可分为分子化合物、离子材料和原子种类。分子化合物主要是润滑剂、润滑脂、光刻胶、溶剂残留物、去离子水中的有机化合物、指纹或塑料储存容器中的有机蒸汽的颗粒或薄膜以及无机化合物。离子材料主要包含来自无机化学物质的阳离子和阴离子,这些无机化学物质可以被物理吸附或化学键合(化学吸附),例如钠离子、氟离子和氯离子。原子或元素种类包括金属,例如铜和重金属,它们可以从含氢氟酸(HF)的溶液电化学镀在半导体表面上,或者它们可以由硅颗粒、灰尘、纤维或来自设备的金属碎片组成。
颗粒可能来自设备、加工化学品、因素操作员、气体管道、晶圆处理和薄膜沉积系统的空气传播灰尘。用于液体的机械(移动)设备和容器是特别多的来源,而固体材料、液体、气体、化学物质和环境空气往往造成较少的颗粒污染,但所有这些都会显著地导致化学杂质的产生。
晶片清洗和表面处理的目的是从半导体表面去除颗粒和化学杂质,而不会损坏或有害地改变衬底表面。晶片表面不得受到粗糙度、点蚀或腐蚀影响,从而抵消清洗过程的结果。等离子体、干物理、湿化学、气相和超临界流体方法可用于实现这些目标。然而,在形成金属导线之前,最广泛使用的和传统的晶片清洗和表面处理方法是基于通常使用过氧化氢混合物的水化学工艺。过去25年来,这种方法取得了成功。 这种类型最著名的系统被称为“RCA清洗过程”,这将在本文中描述。它用于在加工的初始阶段清洗硅片。这些晶片的特征仅在于具有或不具有二氧化硅和氮化硅层或图案的单晶硅或多晶硅,没有暴露的金属区域。含水溶液的反应性化学物质可用于清洁和调节这些耐腐蚀材料。早期清洁通常在栅极氧化物沉积和高温处理(例如热氧化和扩散)之前进行。在这些工艺步骤之前消除污染物对于防止杂质扩散到衬底材料中尤其重要。
在“生产线后端”(BEOL)清洗晶片(稍后在处理过程中进行)的限制要大得多,因为金属区域可能会暴露出来,例如铜、铝或钨金属化,可能还会结合低密度或多孔低介电常数介质膜。基于等离子辅助化学、化学气相反应和低温气溶胶技术的干洗方法可用于去除有机残留物和颗粒污染物。也可以使用水/有机溶剂混合物和其他不会侵蚀暴露的敏感材料的创新方法。
RCA清洁流程的讨论将包括以下处理顺序:
1)初步净化
2)RCA清洁
3)标准清洁- 1 (SC-1)
4)标准清洁- 2 (SC-2)
5)对SC-1/SC-2的修改
6)高频-最后
初步净化
图案化后包括光致抗蚀剂掩模在内的总杂质的去除可以通过干法或液相法来完成。通常使用氧基等离子体的反应等离子体辅助清洗是最广泛使用的干法,这种方法已经在集成电路制造中常规使用多年。几种类型的等离子体源可商购获得。离子引起的对衬底器件晶片的损坏一直是一个问题,但可以在一定程度上得到控制。
液相处理通常用于完成等离子体灰化步骤,或者可以用来完全代替它。它基于将晶片浸入98% H2SO4和30% H2O2的混合物中.在100-130℃的温度下使用2∶1至4∶1的体积比10-15分钟。有机物通过湿化学氧化被破坏和消除,但无机污染物如金属不会被解吸。清洁步骤后的硅表面被硫酸中的硫残留物严重污染。这些“硫酸-过氧化物混合物”(SPM),也被称为“食人鱼蚀刻”(因为它们贪婪地清除有机物的能力),在工厂里处理是危险的;需要护目镜、面罩和塑料手套来保护操作人员。需要用去离子水剧烈冲洗,以完全去除粘性液体。最后,在水冲洗步骤之后,有利的是通过将晶片浸入稀氢氟酸HFH2O(1∶50)中15秒,然后用阿迪水冲洗,剥离裸硅上的含杂质形成的氧化膜。可以通过向SPM中添加微量的HF来进行改性,从而产生排斥性、更好的除硫、更短的漂洗时间和改善的颗粒消除。
注意:此处包含的信息、建议和意见仅供参考,仅供您考虑,查询和验证,不以任何方式 保证任何材料在特定下的的适用性。华林科纳CSE对以任何形式、任何情况,任可应用、测试或交流使用提供的数据不承担任何法法律表任,此处包含的所有内容不得解释为在任何专利下运营或侵如任何专利的 许可或授权。