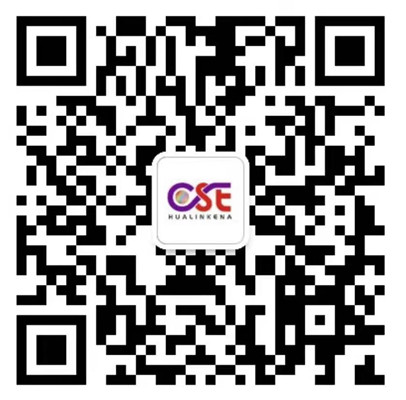
扫码添加微信,获取更多半导体相关资料
介绍
使用氢氧化钾、氢氧化四甲基铵或焦链烯对晶体进行碱性蚀刻,以在微机电系统(微电子机械结构、太阳能电池和集成电路制造)中创建各种特征定义。KOH将在本节中讨论。碱性化学物质具有优先沿着晶体取向蚀刻硅的能力。这使得用其他微加工技术(例如V形槽)制造难以制造的几何形状成为可能。蚀刻速率取决于硅晶面的取向,由于原子在这些取向上的排列,< 100 >和< 110 >的取向蚀刻不同于< 111 >的取向。硅< 100 >沿< 111 >晶面各向异性蚀刻,与< 100 >面成54.74°角。硅< 100 >被掩蔽蚀刻。
加工工艺学
氢氧化钾溶液是通过将氢氧化钾小球溶解在去离子超纯晶片(去离子H2O)中制备的。提出了各种浓度的蚀刻溶液,有时使用添加剂来降低表面粗糙度;硅的蚀刻速率取决于氢氧化钾溶液的浓度。氢氧化钾蚀刻速率也取决于温度。分批浸没槽控制温度,并能向氢氧化钾溶液中加入水,是首选的处理方法。添加剂通常是有机的,如异丙醇(IPA),在蚀刻过程中添加以平滑表面。
必须避免溶液中的气泡,因为这些气泡会掩盖蚀刻。掩模材料通常是氮化硅(Si3N4)或二氧化硅.金或其他金属也可以用作掩蔽材料。晶片上不应有任何有机材料(如光刻胶),因为这会污染氢氧化钾溶液,因为光刻胶会腐蚀。硅对氮化硅的选择性非常高,为了生产,可以假设氮化硅根本不蚀刻。然而,观察到二氧化硅的氢氧化钾蚀刻;蚀刻速率比硅的蚀刻速率慢得多(1-2个数量级),但在进行深度蚀刻时应予以考虑。选择性取决于温度和浓度。通过调节浓度和温度获得的慢蚀刻速率工艺用于最大化硅对二氧化硅的选择性。硅刻蚀速率与N型材料的掺杂无关;例如P和As,然而,对于P型掺杂,例如B,在较高的掺杂浓度下,< 110 >蚀刻速率降低。
对于硅< 100 >,在大约60℃的温度下,在80%去离子水中20重量%氢氧化钾的浓度下,获得接近20米/小时的蚀刻速率。在不同浓度和温度的氢氧化钾中,硅、氮化硅和二氧化硅的蚀刻速率见参考文献[3] [4]。图2显示了20重量%氢氧化钾溶液的温度与蚀刻速率的关系。在较低浓度下,约20-30%,除了获得较高的剥离速率外,还获得了比较高浓度下更光滑的表面。使用的最大浓度约为60 %,因为随着浓度的增加,蚀刻速率迅速降低。此外,较低的浓度更容易控制,并为刻面蚀刻提供最佳结果。图3显示了浓度和温度对不同硅取向的蚀刻速率的关系。加热溶液会加速蚀刻速度。然而,高于60℃的溶液蒸发水分的速度更快,并且蚀刻速度大于获得可重复结果的合理速度。将氢氧化钾浸没槽工艺优化到所需的器件结果将会产生一个宽的工艺窗口。
钾(钾+)是一种碱金属离子,与钠(钠)一样,对于金属氧化物半导体(金属氧化物半导体)器件或任何依赖长寿命的器件(如太阳能电池)来说,钾是一种极快扩散的寿命杀手。因此,在蚀刻完成后,氢氧化钾蚀刻溶液必须有效地从硅表面清除。建议在氢氧化钾处理后使用SC-1进行RCA型清洗。必须遵守适当的程序,以避免污染实验室其他地方的任何金属离子敏感工艺和设备。此外,氢氧化钾是一种腐蚀性溶液,处理时必须注意安全。
应用程序
太阳能电池
太阳能电池(光伏器件)化学蚀刻单晶硅或多晶硅,以可控地粗糙化具有随机纹理的硅,这为光吸收提供了更多的表面积,从而提高了太阳能电池的效率。
用氢氧化钾或其他碱性溶液进行化学蚀刻的另一个应用是去除称为分流的边缘掺杂。由于磷结和氮结之间的界面不清晰,太阳能电池的效率受到漏电的影响。未受氮化硅表面保护的边缘优先被蚀刻,以提高电气性能。
微电子机械系统
使用各向异性硅蚀刻的例子是声学微机电系统的麦克风结构的形成。麦克风是一种薄膜,由硅基器件顶面上的小手指材料支撑,麦克风后面的硅衬底被完全移除。使用氢氧化钾溶液蚀刻孔比干等离子体工艺更经济。其他微机电系统传感器也使用这种技术。
通信操作指令
存在使用氢氧化钾蚀刻深沟槽以形成岛的可能性,用于SOI材料,例如蓝宝石或二氧化硅绝缘体上的硅。
改造
在研磨和抛光步骤之前,使用氢氧化钾浴剥离多晶硅。在这个过程中,一些单晶硅也被去除。
注意:此处包含的信息、建议和意见仅供参考,仅供您考虑,查询和验证,不以任何方式 保证任何材料在特定下的的适用性。华林科纳CSE对以任何形式、任何情况,任可应用、测试或交流使用提供的数据不承担任何法法律表任,此处包含的所有内容不得解释为在任何专利下运营或侵如任何专利的 许可或授权。