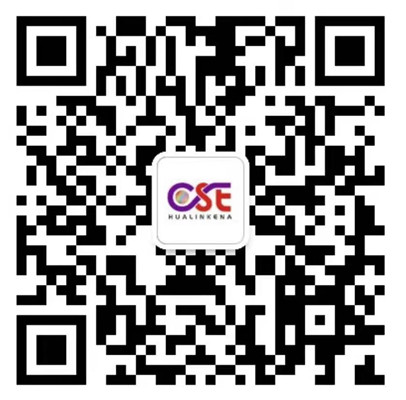
扫码添加微信,获取更多半导体相关资料
温度和浓度控制
基本上有两种方法来控制浸浴中的氮化物蚀刻过程,这两种方法都包括连续加热和补水:
1.恒温加热温度控制和H2O尖峰沸点调节。
这种方法是最常见的控制方式,它使用强大的加热器,能够将介质加热到沸点及以上。加热功率在该过程中不受控制(即。设定在固定的、大部分是最大的设定点)。通过改变H2O补充量,液体浓度被设定为在确定的工艺温度下精确沸腾。因此,温度极限由实际混合物的沸点控制。
这种方法为标准应用程序提供了可接受的性能结果。从投资角度来看,它是最具成本效益的解决方案,可用于自动化和手动(即。简单的过程控制)湿工作台。缺点是在起泡液体中处理晶片,这影响晶片蚀刻的不均匀性,并且经常导致晶片从盒子或保持器中取出,并且产生过量的工艺蒸汽,需要防止其在湿工作台中再次冷凝并且有效通风。此外,整个过程由单个参数控制,这不允许在加载效果和时间上微调变化的蚀刻性能。
2.具有可变功率加热的独立功率和浓度控制。
通过使用由温度传感器控制的具有可变功率的加热系统,浴溶液可以被加热到期望的处理器,同时H2O补充被设置为实现混合物的恒定浓度,以具有略高于工艺温度的沸点。浴缸本身将保持平静,基本上没有泡沫。通过PID控制,加热能够补偿过程变化,即。
由进入槽的冷晶片引起的温度下降,并在整个工艺时间内导致更可再现的蚀刻。此外,在熔池寿命期间的硅负载效应可以根据水脉冲过程通过时间或批次进行补偿。最后,通过流量优化,可以将从储罐底部(加热器通常位于此处)到顶部(与环境温度空气的界面)的垂直温差降至最低,这只有在平静的液体中才有可能。缺点显然是支持控制机制的努力和组件成本较高。
先进器件制造设备通常使用后一种方法来满足产品要求需求,要求不高的产品也可以用第一种方法构建出好的结果。
典型工艺和性能参数
用于选择性氮化物蚀刻的热磷酸浴在半导体中已经非常标准化制造业。最重要的工艺参数如下:
初始浓度(交付的原磷酸): |
| 85重量% |
生产过程中的典型浓度(@ 165℃): |
|
| 87-9重量% |
过程温度: |
|
| 160-165℃ |
温度公差(单一过程): |
|
| ±5℃ |
耐温性(理想浴) |
|
| +- 2摄氏度 |
典型的H2O补给率(200毫米) |
|
| 60-90毫升分钟 |
浴缸再循环(200毫米): |
|
| > 6 gpm |
浴寿命 |
|
| 24 -72小时 |
工艺时间(30纳米Si3N4加上30 %的过蚀刻) |
|
| 10–15分钟 |
在调味浴中,在控制良好的设备中进行的过程可以满足以下性能:
160℃时Si3N4的蚀刻速率 40–44转/分钟
165℃时Si3N4的蚀刻速率 50–55安斯特/分钟
晶片内的不均匀性: 最大/最小5 %
晶片间的不均匀性: 最大/最小3 %
批次间的不一致性 最大/最小5 %
氧化物选择性 >80:1
硅蚀刻 < 0.1安斯特/分钟
污染(包括冲洗/干燥) < 30个加法器(> 0.16米)
注意:此处包含的信息、建议和意见仅供参考,仅供您考虑,查询和验证,不以任何方式 保证任何材料在特定下的的适用性。华林科纳CSE对以任何形式、任何情况,任可应用、测试或交流使用提供的数据不承担任何法法律表任,此处包含的所有内容不得解释为在任何专利下运营或侵如任何专利的 许可或授权。