SiC基芯片背面通孔刻蚀工艺研究
摘要:通过对感应耦合等离子体(ICP)设备装片夹具进行改进,提高了背氦的导热效率,减小了下电极基底与晶圆表面之间的温度差,提高了冷却效果。对装片夹具改进前后进行了对比实验,并分析了射频功率、ICP功率、下电极基底温度、腔室压力等参数对SiC背面通孔的刻蚀速率、选择比、倾斜角及侧壁光滑度的影响。通过装片夹具改进及工艺条件优化,开发出刻蚀速率为1μm/min、SiC与Ni的选择比大于60∶1、倾斜角小于85°、侧壁光滑的SiC通孔工艺条件,可用于SiC基GaN高电子迁移率晶体管(HEMT)、SiC金属半导体场效应管(MESFET)等大功率微波器件及其微波单片集成电路(MMIC)研制与生产的背面通孔刻蚀,并可缩短工艺时间降低生产成本。
关键词:碳化硅;背面通孔刻蚀;感应耦合等离子体(ICP);刻蚀速率;
引言
SiC与GaN为继Si和GaAs材料之后的第三代半导体材料的典型代表,用其制作的半导体微波功率器件及其微波单片集成电路(MMIC)具有工作温度高、应用频率高、功率输出大、增益高等优点[1-2]。由于SiC材料具有较高的热导率和稳定性及与GaN材料的晶格匹配较好,在SiC衬底上外延GaN材料成为当今GaN功率器件发展的主要方向,特别是在高性能GaN高电子迁移率晶体管(HEMT)微波功率器件及其MMIC领域,目前基本是采用SiC衬底上外延GaN材料[3]。为了减小器件源端寄生电感,GaN和SiC的微波功率器件均需采用通孔接地的形式,以尽可能改善器件的频率特性[4]。无论是SiC基GaNHEMT及其MMIC,还是SiC金属半导体场效应管(MESFET)及其MMIC,其背面通孔工艺主要刻蚀材料均为SiC材料,SiC基芯片背面通孔刻蚀工艺成为提高器件频率特性和可靠性的关键工艺之一。而SiC材料具有化学性质稳定、键能高等特点,目前尚无公开报道的成熟的湿法腐蚀技术,干法刻蚀方法主要有反应离子刻蚀(reactiveionetching,RIE)、电子回旋共振(electroncyclontronresonance,ECR)刻蚀、感应耦合等离子体(inductivelycoupledplasma,ICP)刻蚀等,由于ICP刻蚀具有更高的等离子密度、更高的等离子能量、更优异的散热结构和等离子密度及能量可以独立控制的优点,采用ICP刻蚀SiC较其他方法具有刻蚀速率快、均匀性好、一致性好等优点。以往刻蚀SiC面临的主要问题有三点:一是刻蚀速率低,不能满足日益增长的产能需求;二是依靠增加射频功率,虽能提高刻蚀速率但选择比下0降严重,不能满足生产需求;三是提高下电极基底温度也能提高刻蚀速率但随之刻蚀聚合物增多,聚合物增加到一定程度会在刻蚀底部形成一层微掩膜造成刻蚀速率下降。周瑞等人[5]通过优化气体组分、气体压力等使SiC通孔刻蚀速率达0.7μm/min,SiC与Ni的刻蚀选择比为60∶1。A.Barker等人[6]报道了采用环形耦合射频输出和多级磁性增强等离子密度的方法实现了刻蚀速率为1.3μm/min,SiC与Ni的刻蚀选择比为35∶1的结果。
通过各种方式增加等离子密度或能量进而提高刻蚀速率是刻蚀工艺普遍采用的主要方法之一,而无论是增加等离子密度还是能量,均会造成刻蚀过程中晶圆表面温度的升高,随晶圆表面温度升高上述提到的刻蚀聚合物问题就会凸显,因此刻蚀过程中的冷却一直是刻蚀工艺研究的热点。国际及国内对该冷却的研究主要集中在通过使用新型冷却液、新型冷却方式(如液氮等)等降低下电极的极限温度(甚至低达-100℃以下),进而降低晶圆表面的温度,但晶圆表面温度降低的效果并不理想[7]。本文所用ICP设备采用冷却液冷却,冷却液下限温度为0℃,下电极与晶圆之间通氦气以提高冷却效果,本研究通过对ICP装片夹具进行改进,提高了冷却效果。通过装片夹具改进及工艺条件优化,实现了刻蚀速率与选择比同时提升、侧壁聚合物明显减少、刻蚀倾斜角低于85°的较为理想的SiC通孔工艺条件。
1实验设计
1.1样品制备
在4H-SiC高纯半绝缘衬底材料上通过溅射基层金属、光刻图形、电镀加厚金属掩膜(掩膜Ni厚度为3μm)的流程制作出刻蚀图形为25μm×50μm的矩形待刻蚀样品,将该样品通过砂轮划片机划成1cm×1cm的矩形样品待用,每次刻蚀前将其粘在厚度为3mm直径为3英寸(1英寸=2.54cm)蓝宝石基片上,为减小蓝宝石基底对刻蚀结果的影响并使实验过程尽可能与实际工艺接近,蓝宝石衬底上均通过上述工艺流程电镀厚度为3μm的Ni掩膜。
1.2实验过程
刻蚀SiC实验主要采用SF6气体,为了研究装片夹具改进前后对刻蚀结果的影响,使用两种夹具进行了对比实验,分析了不同下电极基底温度、不同腔室压力、不同RF功率、不同ICP功率等工艺参数对刻蚀结果的影响(温度变化范围设定值±0.5℃,腔室压力、RF功率、ICP功率变化范围设定值±1%,RF反射功率、ICP反射功率变化范围为正向功率设定值的±2%以内),工艺过程中晶圆表面温度由变温试纸直接测试,下电极基底温度由温控设备控制(温度变化范围设定值±0.5℃)。本实验在基准工艺条件(温度10℃,腔室压力1.33Pa,RF功率150W,ICP功率1500W)基础上,分别固定其他工艺参数,变化单一工艺参数得出其对刻蚀速率(刻蚀深度与刻蚀总时间的比值)、选择比(SiC刻蚀速率与掩膜Ni刻蚀速率比值)、倾斜角和侧壁光滑度的影响。1.3结果表征通过扫描电子显微镜(SEM)观测样品刻蚀后表面聚合物残留情况、刻蚀后的倾斜角和侧壁光滑度;使用台阶仪测试样品刻蚀后的刻蚀深度。
2结果及讨论
图1为装片夹具结构改进前后对比图,改进后的装片夹具最大不同在于在金属压块与晶圆之间增加了一密封圈。

图2,图3和图4分别为改进夹具前后RF功率(PRF)、ICP功率(PICP)、下电极基底温度(tsub)(金属压块下的温度)对刻蚀速率(v)和选择比(Rsel)的影响曲线。从图中可以看出,在改进夹具之前,刻蚀速率并没有随RF和ICP功率增加而一直增加,而是RF和ICP功率增加到一定程度后,随功率增加刻蚀速率反而下降,并且刻蚀速率随下电极基底温度变化也呈现相同的变化趋势。使用改进后的夹具,刻蚀速率随RF功率、ICP功率的增加而增加,刻蚀速率随下电极基底温度依然呈现先升高再下降的规律,但拐点温度(刻蚀速率开始下降的温度点定义为拐点温度)由改进前的约15℃增加到改进后的25℃左右。这是因为改进后的夹具在压块边缘制作了一沟槽,在压块与晶圆之间增加了一密封圈,这可以有效减弱高压背氦泄漏到真空腔室内,压块与晶圆之间的导热氦气增多,使压块与晶圆之间的有效导热效率提升,从而有效提高了冷却效果,降低了工艺过程中晶圆表面温度,温度过高是改进夹具前RF功率、ICP功率、衬底温度增加到一定程度后刻蚀速率反而下降的原因。图5和图6显示了改进夹具前后不同RF功率、不同下电极基底温度下工艺过程中晶圆表面的实际温度,该温度是用变温试纸直接测量的,从图中可以看出,改进夹具后晶圆表面温度都大幅下降,温度过高刻蚀速率下降是因为刻蚀聚合物的增多阻止了进一步的刻蚀[8-9],图7的SEM照片也证实了这一点。
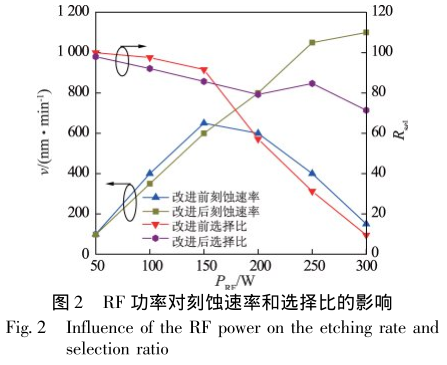


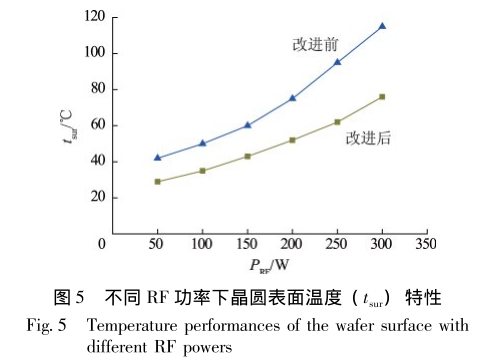


为得到较为理想的SiC通孔刻蚀条件,基于改进后的夹具,系统进行了RF功率、ICP功率、下电极基底温度、腔室压力、气体流量等参数对刻蚀速率、选择比、侧壁倾斜角、侧壁光滑度的影响实验。
验结果表明,提高RF功率可以大幅提高刻蚀速率,降低侧壁倾斜角,但选择比下降,侧壁聚合物随之增多,这是由于RF功率的增加导致腔室内等离子动能增加,物理轰击效果加强,刻蚀SiC和掩膜Ni的速率显著增加,但掩膜Ni的刻蚀速率增加更快,导致选择比降低,倾斜角下降,同时侧壁聚合物增多;提高ICP功率可以大幅提高刻蚀速率和选择比,但侧壁倾斜角变陡,侧壁聚合物增多,这是由于ICP功率的增加导致腔室内等离子密度增加,化学作用加强,刻蚀SiC速率显著增加,但对刻蚀掩膜Ni的速率影响不大,导致选择比升高,倾斜角增加,聚合物增加;下电极基底温度的影响前文已做详细论述,此处不再赘述;提升腔室压力,可以减少侧壁聚合物,但刻蚀速率及选择比均有所下降,其对侧壁倾斜角影响不大,这是由于随腔室压力的升高,等离子间的碰撞加剧,离子平均自由程减小,离子动能减少,刻蚀SiC和掩膜Ni速率均下降,但SiC刻蚀速率下降更快,导致选择比下降,侧壁聚合物减少,而侧壁倾斜角变化不明显;随SF6流量增加,侧壁聚合物明显减少,但刻蚀速率是先提高后降低,选择比亦呈现相似的变化,其对侧壁倾斜角影响不大,这是因为随气体流量增加,初期可以有效增加等离子密度,但随着气体流量的增加离化率变差,再增加的气体成为稀释气体,不能对SiC实现有效刻蚀,导致刻蚀速率和选择比先提高后降低,但增加的气体可以有效保护侧壁,减少侧壁聚合物,而侧壁倾斜角变化不明显。采用新夹具通过优化各个工艺参数实现了刻蚀速率与选择比同时提升、侧壁聚合物明显减少、刻蚀倾斜角降低的目的。图7(a)和(b)分别为使用改进前和改进后夹具的通孔刻蚀SEM图片,通过该对比图片可以看出,采用新夹具、优化各工艺条件后的刻蚀聚合物明显减少。最终得出刻蚀速率大于1μm/min、刻蚀选择比大于60∶1、倾斜角小于85°、侧壁光滑的工艺条件,该工艺条件具体应用在某产品的通孔剖面图见图8,从图中也可以看出通孔侧壁实现了良好的金属覆盖。
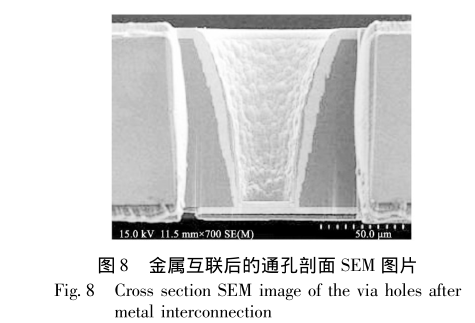
3结论
工艺温度是影响SiC通孔刻蚀结果的一个重要因素,通过对ICP装片夹具进行改进,提高冷却效果,刻蚀过程中晶圆表面温度降低。再经过对设备的RF功率、ICP功率、下电极基底温度、腔室压力等工艺条件优化,开发出刻蚀速率大于1μm/min、SiC与Ni的选择比大于60∶1、倾斜角小于85°、侧壁光滑的SiC通孔工艺条件,这一技术适用于SiC基GaNHEMT和SiCMESFET等大功率微波器件及其MMIC研制与生产的背面通孔刻蚀,并可缩短工艺时间降低生产成本。(免责声明:文章来源于网络,如有侵权请联系作者删除。)